Kaum ein Messverfahren
gibt so schnell Aussagen zur Zustandsanalyse von elektrischen Schaltanlagen
in allen Spannungsebenen. Werden diese Überprüfungen nicht rechtzeitig und
turnusmäßig durchgeführt, so wird man durch diese Versäumnisse meistens im
Nachhinein bestraft.
Auch die Korona- Messungen (Teilentladungsmessungen) werden im Hochspannungsbereich oft benötigt
und geben wichtige Aussagen, über den Zustand von vieler elektrischen Anlagen (s.unten).
|
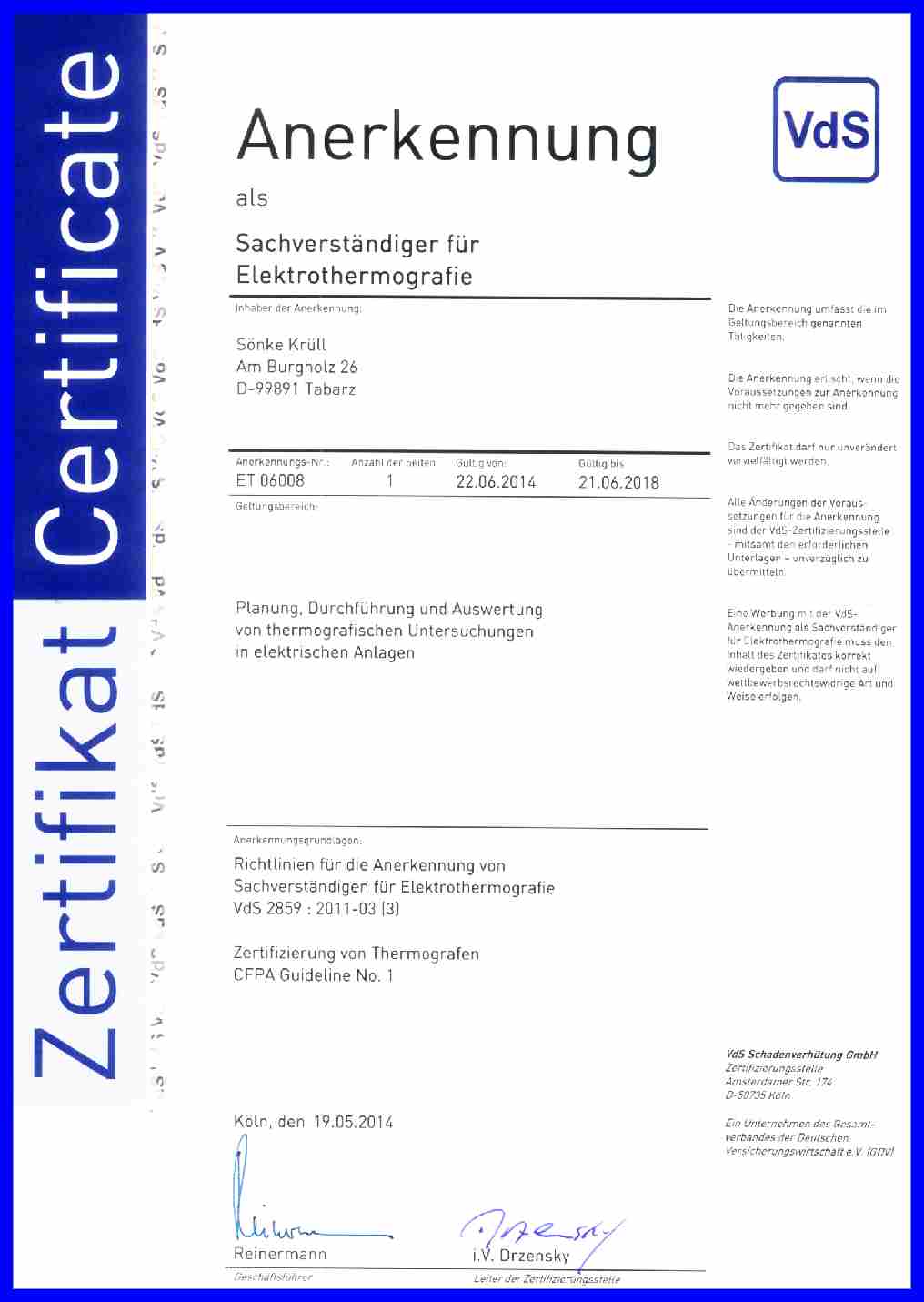
|
VdS - Zertifikate zur
Anerkennung als Sachverständige für Elektrothermografie
Zertifikat
Nr.: ET 06008
gültig bis 21.06.2026 (Sönke Krüll)
Zertifikat als pdf- Datei
Zertifikat
Nr.: ET 23004
gültig bis 16.07.2027 (Maik Rudolph)
Zertifikat als pdf- Datei
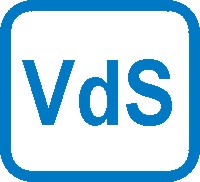
|
Thermovision an elektrischen Schaltanlagen, auch
Thermografie / Thermographie genannt, werden von den Energieversorgungsunternehmen
bereits seit sehr vielen Jahren durchgeführt. Durch regelmäßige Kontrollen
mit Infrarottechniken wird erreicht, dass eine hohe Verfügbarkeit der
elektrischen Anlagen und somit der Stromversorgung gewährleistet ist. Auch
in sehr vielen Betrieben werden diese vorbeugenden Instandhaltungsmaßnahmen
durchgeführt. Durch regelmäßigen Infrarotmessungen
ergeben sich wirtschaftliche Nutzeffekte, welche die
Brandschutzversicherungen zusätzlich durch eine Senkung der
Versicherungsbeiträge honorieren. Um die Gefahren zu minimieren und
Fehlmessungen und Fehlinterpretationen vom Messpersonal
weitestgehend auszuschließen, hat die Versicherungswirtschaft darauf
gedrungen, dass der VdS
Schadenverhütung eine Zertifizierung von Elektrofachkräften nach DIN
VDE 1000-10 und Elektroingenieuren zum "VdS
anerkannten Sachverständigen für Elektrothermografie VdS
2859: 2005-01" durchführt. Diese Zertifizierungen werden seit dem
Jahr 2005 vom VdS angeboten und nach einer
einwöchigen Schulung und bestandener Prüfung vergeben. Seitens der
Versicherungswirtschaft wird dieses Zertifikat seit einigen Jahren
gefordert.
Zweck
und Nutzen der Thermografie:
- Dokumentation von Anlagenzuständen und potentiellen
Risiken
- Früherkennung von Schwachstellen und Schäden
- Erhöhung der Anlagenverfügbarkeit und
-zuverlässigkeit
- Vermeidung von Folgeschäden
- Reduzierung der Brand- und Unfallgefahren
Durch den VdS
(Gesamtverband der Deutschen Versicherungswirtschaft e.V., Büro
Schadenverhütung) wird die Prüfung von elektrischen Anlagen durch die VdS 2858 näher beschrieben.
Danach sind elektrische Anlagen vom Betreiber regelmäßig zu prüfen
(wiederkehrende Prüfungen), z.B. gemäß:
- Technischer Prüfverordnungen des jeweiligen
Bundeslandes,
- BGV A3 (Unfall- Verhütungs- Vorschrift (UVV) der Berufsgenossenschaften),
- DIN VDE 0105, bei der der "ordnungsgemäße
Zustand der elektrischen Anlage" festzustellen ist,
- Feuerversicherungs- Klausel (Klausel 3602), die
zusätzlich eine Prüfung nach den Sicherheitsvorschriften der
Feuerversicherungen verlangt.
Die Thermografie kann die
vorgenannten wiederkehrenden Prüfungen nicht ersetzen. Sie ist auch kein
Ersatz für die notwendigen Sichtkontrollen, Funktionsprüfungen,
Strommessungen usw., die im Rahmen der vorgenannten wiederkehrenden
Prüfungen durchgeführt werden müssen. Sie stellt jedoch eine hilfreiche,
ergänzende Messmethode
dar und ermöglicht insbesondere Untersuchungen und Bewertungen des
Anlagenzustandes, die bislang nur schwer oder mit hohem Aufwand möglich
waren. Ein großer Vorteil ist, dass die Messungen bei laufendem Betrieb,
also unter Spannung durchgeführt werden können. Thermografie gehört heute
zum Stand der Sicherheitstechnik.
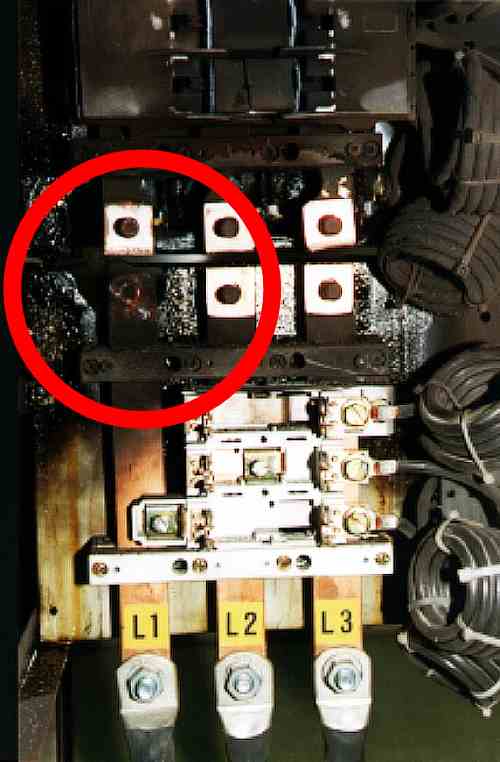
|
. . . . . . . .
|
Rund 35% aller Betriebsbrände entstehen durch
thermische Erhitzungen von elektrischen
Anlagen. Bereits nach der zweiten thermografischen Untersuchung sinkt die
Ausfallquote um 80%.
Das linke Foto zeigt die Kompensation einer 0,4 kV
Anlage welche ausbrannte, da an der Schraubverbindung am Leiter L1
(innerhalb des roten Kreises) der Übergangswiderstand durch eine lose
Verbindung so groß wurde, dass die Verbindungsstelle zu glühen begann und
somit den Schrank in Brand setzte. Zum Glück beschränkte sich der Brand
in diesem Fall auf den Schrank, da er weit genug von anderen brennbaren
Gegenständen entfernt stand. Nach diesem Brandfall legte man in dem
betreffenden Industriebetrieb, auch auf Drängen der Versicherung fest,
jährlich Infrarotaufnahmen zum vorbeugenden Brandschutz durchzuführen.
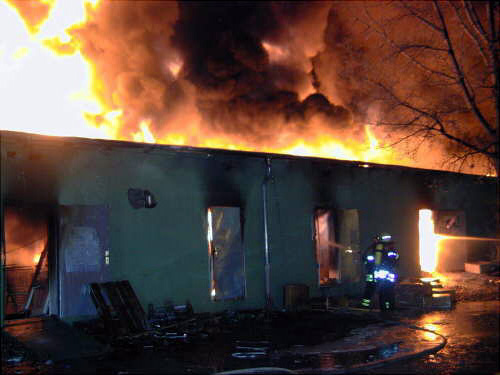
Quelle:
www.feuerwehr-erfurt.de/
|
Die beiden unteren Bilder zeigen einen 110 / 10 kV Transformator. Im linken Infrarotbild (vor 20
Jahren mit einer heute veralteten Kameratechnik aufgenommen) kann man an
der linken Trafodurchführung eine Temperatur
von 80,9°C messen. Als erstes wurde vermutet, dass die Schraubverbindung
auf der Trafodurchführung fehlerhaft war.
Genauere Untersuchungen, wie die Öl - Gasanalyse
ergaben, dass die Verbindung innerhalb des Trafos
fehlerhaft war und ausgewechselt werden musste.
Die größte, von uns gemessene Temperatur an 110kV Anlagen, betrug bisher
530°C bei einer Belastung von nur 27%. Die Hochrechnung ergab, dass bei
Nennbelastung (Engpassstrom) die davon betroffene Schraubverbindung der
110kV - Leitung eine Temperatur von ca. 3.000°C aufweisen würde. Diese
hohe Temperatur würde allerdings nie erreicht werden, da das Aluminium
bereits bei ca. 660°C schmilzt und damit die Stromversorgung unterbricht.
Die Kosten, besonders durch den Stromausfall, können wenn viele
Industriebetriebe davon betroffen sind, für die
Energieversorgungsunternehmen sehr hoch werden.
|
|
|
|
|
|
|
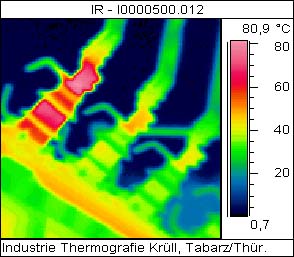
|
. . . . . . . .
|

|
Leiter
|
|
:
|
L1
|
L2
|
L3
|
|
Nennlast
|
(A)
|
:
|
1.375
|
1.375
|
1.375
|
|
Belastung
während der Messung
|
(A)
|
:
|
920
|
920
|
920
|
|
Belastung
in Prozent
|
(%)
|
:
|
67
|
67
|
67
|
|
maximale
Objekttemperatur
|
(°C)
|
:
|
43
|
43
|
81
|
|
gemessene
Übertemperatur
|
(D T in K)
|
:
|
-
|
-
|
38
|
|
Temperatur
bei Nennlast
|
(°C)
ca.
|
:
|
-
|
-
|
160
|
|
Fehlergruppe
|
(1
- 4)
|
:
|
-
|
-
|
3
|
|
|
|
|
|
|
|
|
|
|
|
In Auswertung des oberen Infrarotbildes von der Trafodurchführung gibt die Tabelle einen Überblick
über die Belastung der einzelnen Leiter während der Messung. Bei einer
Belastung von 67% der Nennlast betrug die
Temperatur am Oberteil der Kerze 81°C. Wenn man diese Temperatur auf Nennlast (Engpassstrom) hochrechnet, würde sich eine
Temperatur von ca. +160°C im oberen Teil der Trafodurchführung ergeben. An der direkten Fehlerstelle
natürlich noch bedeutend höher.
Generell sind solche Fehler, die nicht direkt einsehbar sind, sehr schwer
abzuschätzen. Aufgrund der reinen Übertemperatur erfolgt eine
Fehlergruppeneinteilung in die Fehlergruppe 3, obwohl die Einteilung in
die Gruppe 4 richtiger gewesen wäre.
Nach dem Öffnen des Transformators war der große Schaden entsprechend des
nebenstehenden Fotos zu erkennen. Es ist sehr gut zu erkennen, dass das
erste Dehnungsband schon weggebrannt ist und von einer Schraubverbindung
kaum noch gesprochen werden kann. Lange hätte es nicht mehr gedauert, und
das Dehnungsband zur Durchführung im inneren des Transformators wäre
durch die hohen Temperaturen völlig durchgebrannt. In diesem Fall wäre
die Stromversorgung eines größeren Stadtteils unterbrochen worden. Die
Reparaturkosten belief sich auf 85.000,- EUR.
Bei einem unerwarteten längeren Stromausfall wären die Kosten noch viel
höher geworden.
|
. . . . . . . .
|
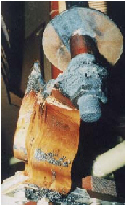
|
|
Erwärmung einer Fehlerstelle innerhalb
eines Jahres um mehr als das Doppelte
Da die untere Fehlerstelle aus betrieblichen
Gründen nicht gleich beseitigt werden konnte, wurde ein Jahr später nach
erneuter turnusmäßiger Kontrolle der gesamten elektrischen Anlage die
Fehlerstelle natürlich erneut lokalisiert. Nach einem Jahr ist die
Temperatur bei gleichbleibender Belastung auf über das Doppelte
angestiegen. Auch diese beiden Infrarotbilder sind älteren Datums und in
ihrer Auflösung nicht mit den jetzigen Infrarotbildern zu vergleichen.
In der darunter liegenden Tabelle ist die Hochrechnung auf Nennlast für diesen thermischen Fehler ersichtlich.
Die beiden unteren Infrarotbilder entstanden schon vor 20 Jahren mit
einer heute nicht mehr zeitgemäßen Technik. Es sind jedoch interessante
Beispiele, welche nur selten zu bekommen sind. Vor 20 Jahren war dies
jedoch "Stand der Technik".
|
maximale Temperatur 68°C am 22.03.1996
|
. . .
|
maximale Temperatur 136°C am 26.02.1997
|

|
. . . . . . . .
|

|
Leiter
|
|
:
|
L1
|
L2
|
L3
|
Nennlast
|
(A)
|
:
|
1.000
|
1.000
|
1.000
|
Belastung
während der Messung
|
(A)
|
:
|
500
|
500
|
500
|
Belastung
in Prozent
|
(%)
|
:
|
50
|
50
|
50
|
maximale
Objekttemperatur
|
(°C)
|
:
|
136
|
35
|
35
|
gemessene
Übertemperatur
|
(D T in K)
|
:
|
101
|
-
|
-
|
Temperatur
bei Nennlast
|
(°C)
ca.
|
:
|
400
|
-
|
-
|
Fehlergruppe
|
(1
- 4)
|
:
|
4
|
-
|
-
|
|
|
|
|
|
|
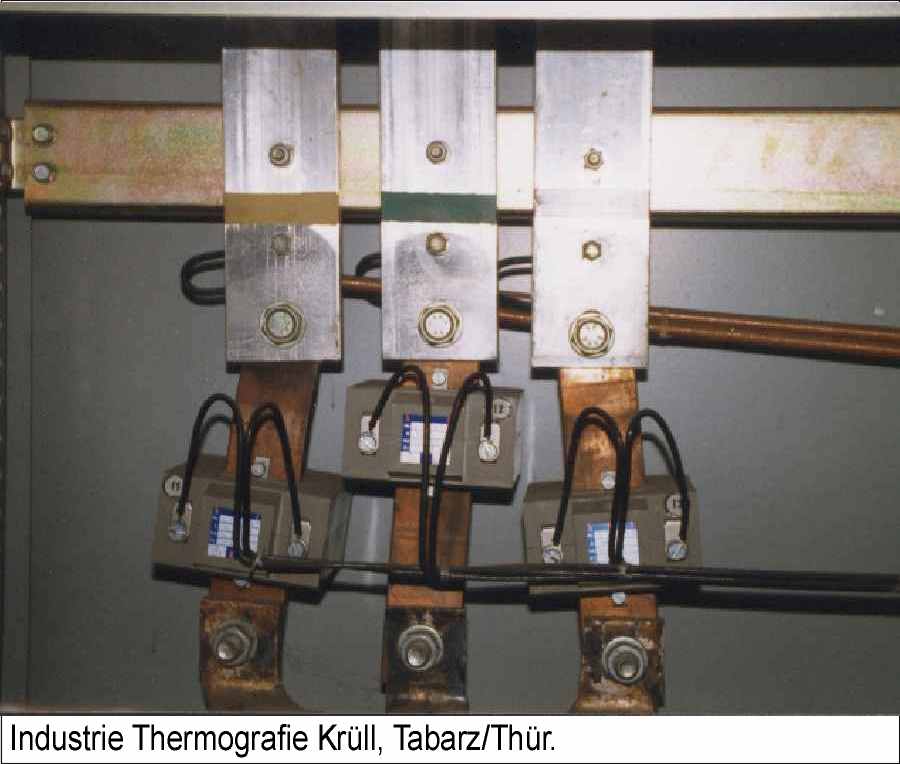
|
. . . . . . . .
|
Originalfoto der im Infrarotbild dargestellten
Schwachstelle aus dem Jahre 1997. An dem Aluminium und dem Kupfer oder
auch an den Schrauben ist keine Erwärmung oder Verfärbung zu erkennen.
Kupfer und Aluminium direkt miteinander verbinden
sollte man vermeiden, da durch das so entstehende galvanische Element
(liegen in der Spannungsreihe im Periondensystem
sehr weit auseinander) stets mit Problemen zu rechnen ist. Wenn dann auch
noch Feuchtigkeit erwartet wird, sind Probleme vorprogrammiert. Wenn eine
derartige Verbindung nicht zu umgehen ist, so können sogenannten AlCu- Scheiben eingesetzt werden. Diese besitzen auf
der einen Seite eine Kupfer- und auf der anderen Seite eine Aluminium-
Fläche.
|
|
Oft sind es nur Kleinigkeiten, welche Maschinenausfälle
oder im schlimmsten Fall Brände verursachen. Das untere Foto mit dem
dazugehörigen Infrarotbild zeigen lose Kabel an einem 0,4kV
Hauptschalter. Mit dem Auge ist noch keine Verfärbung der Isolierung
wahrzunehmen. Ein Zeichen dafür, dass die Fehlerstelle noch nicht lange
vorhanden ist. Oft sind es lose Klemmstellen, welche den
Übergangswiderstand ansteigen lassen und es somit zu der Erwärmung kommt.
Ein Nachziehen der Verbindungsstellen behebt, bei diesem meist
Kupferkabel und den geringen Temperaturen, den Fehler im Regelfall. Ist
die Temperatur höher, so müssen die Anschlusskabel nachgesetzt oder
ausgetauscht werden. Auch ein Austausch, wie in diesem Beispiel der
Schalter kann sich dann erforderlich machen.
|
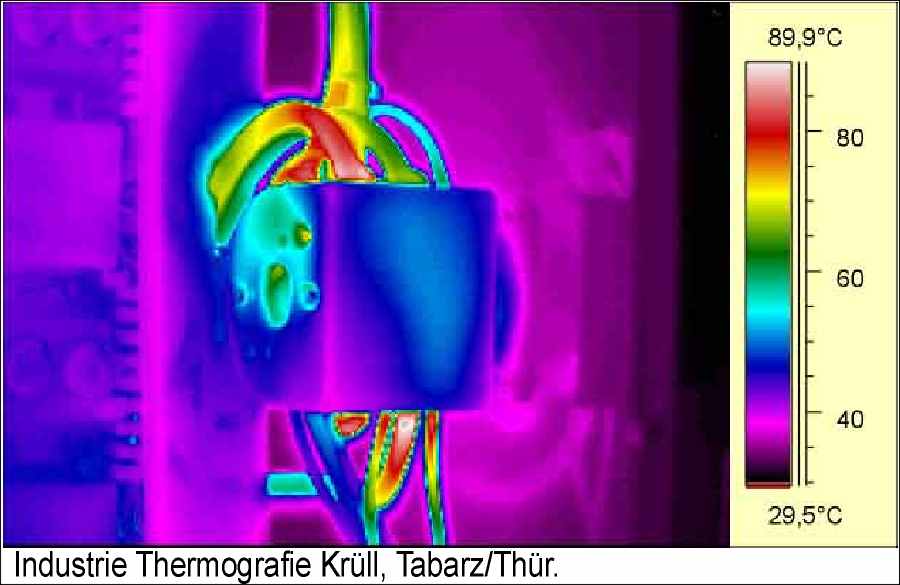
|
. . . . . . . .
|
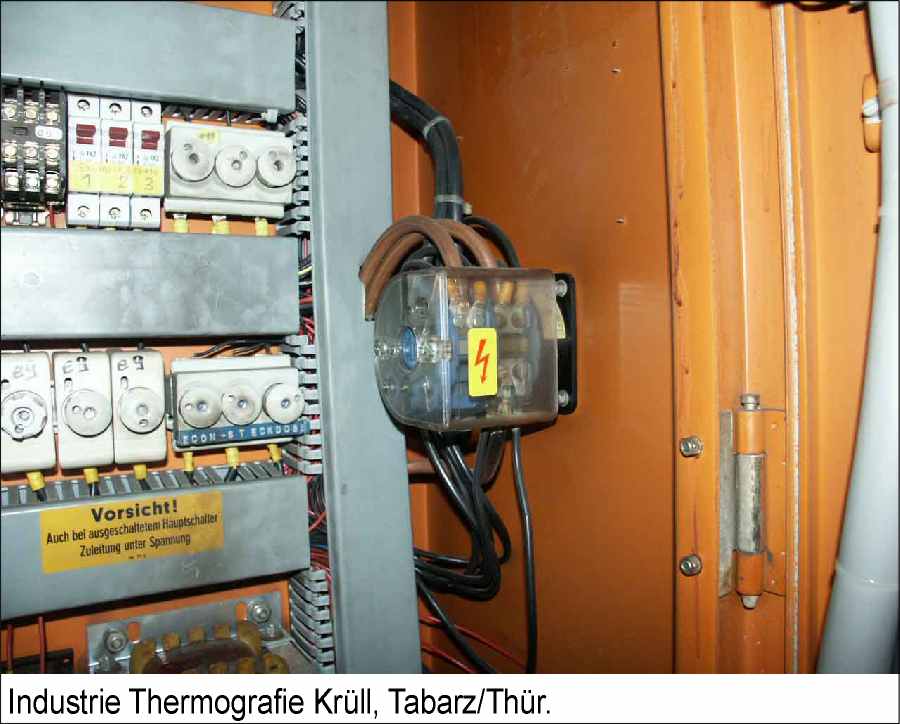
|
|
|
|
|
Am unteren Schraubsicherungselement der
Lichtverteilung ist bei einer Umgebungstemperatur von nur 13°C eine
Temperatur von fast 400°C zu messen. Äußerlich ist die hohe Temperatur
der Sicherung nicht zu erkennen. Womöglich war die Schraubsicherung nicht
fest genug angezogen. Diese Schraubsicherungen neigen sehr schnell dazu
heiß zu werden, wenn der Kontaktdruck nicht hoch genug ist. Manchmal ist
auch der Kabelanschluss am Sicherungsfuß für die Erwärmung
verantwortlich. Ein Austausch des gesamten Sicherungselementes mit der
Halterung ist hier notwendig. Auch der Kabelanschluss ist zu
kontrollieren und ggf. das Kabel auszutauschen oder nachzusetzen.
|
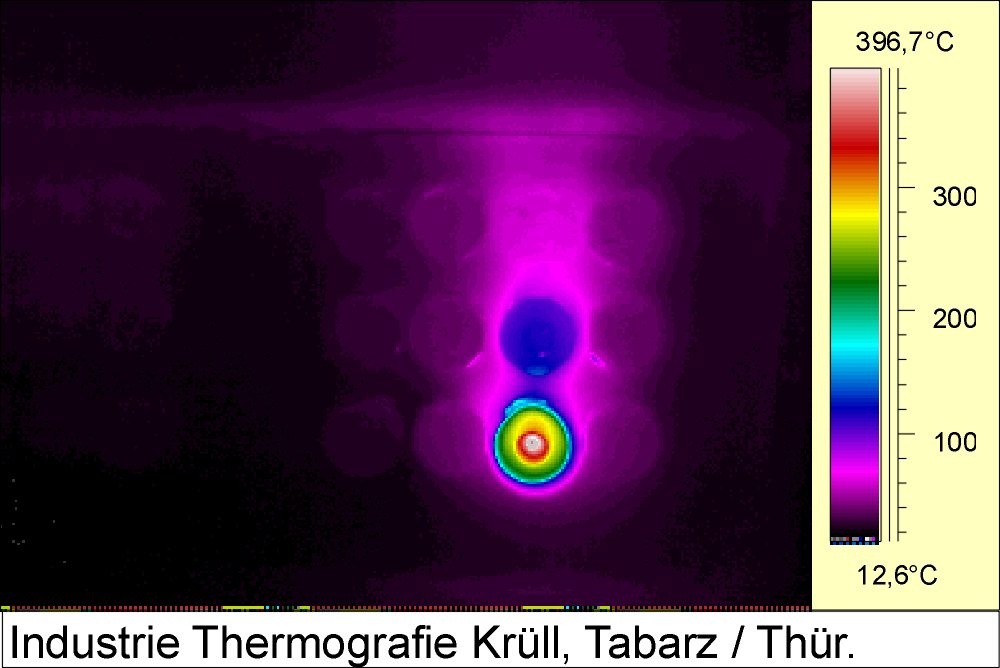
|
. . . . . . . .
|
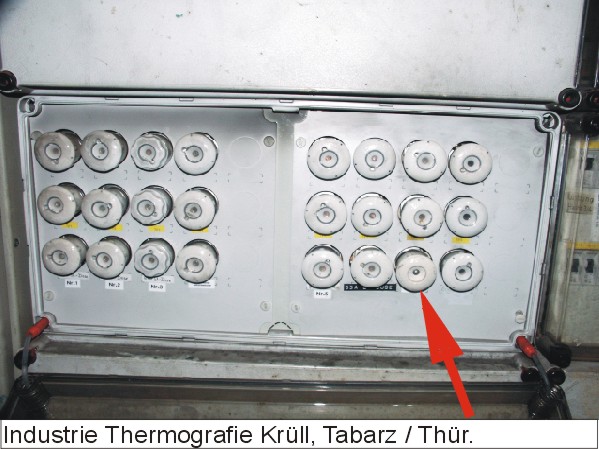
|
|
An dieser 0,4kV NH- Sicherung (Leiter L2) wurden an
der oberen Kontaktzunge 403°C gemessen. Ein unzureichender Federkontakt
wird hier die Ursache für diese starke Erwärmung gewesen sein. Im
Originalbild ist bereits eine starke Verfärbung der Kontakte zu erkennen.
Der Kunststoffschutzschlauch über der Sicherung fängt bereits an sich
aufzulösen. Hier muss unverzüglich gehandelt werden, um einem Brand
vorzubeugen und Produktionsausfall entgegenzuwirken. Ein Austausch von
Sicherungshalter, Sicherung und auch dem Zuleitungskabel ist notwendig.
|
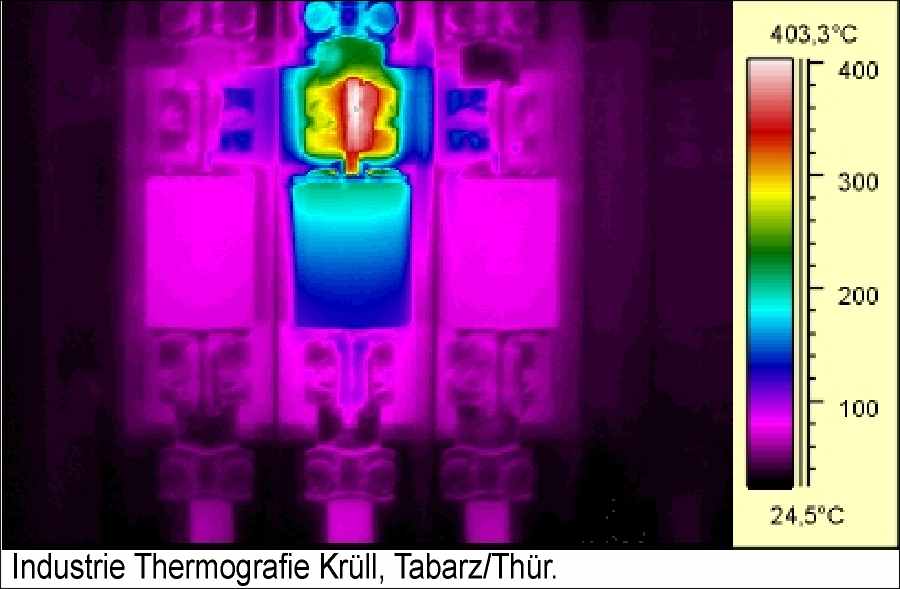
|
. . . . . . . .
|
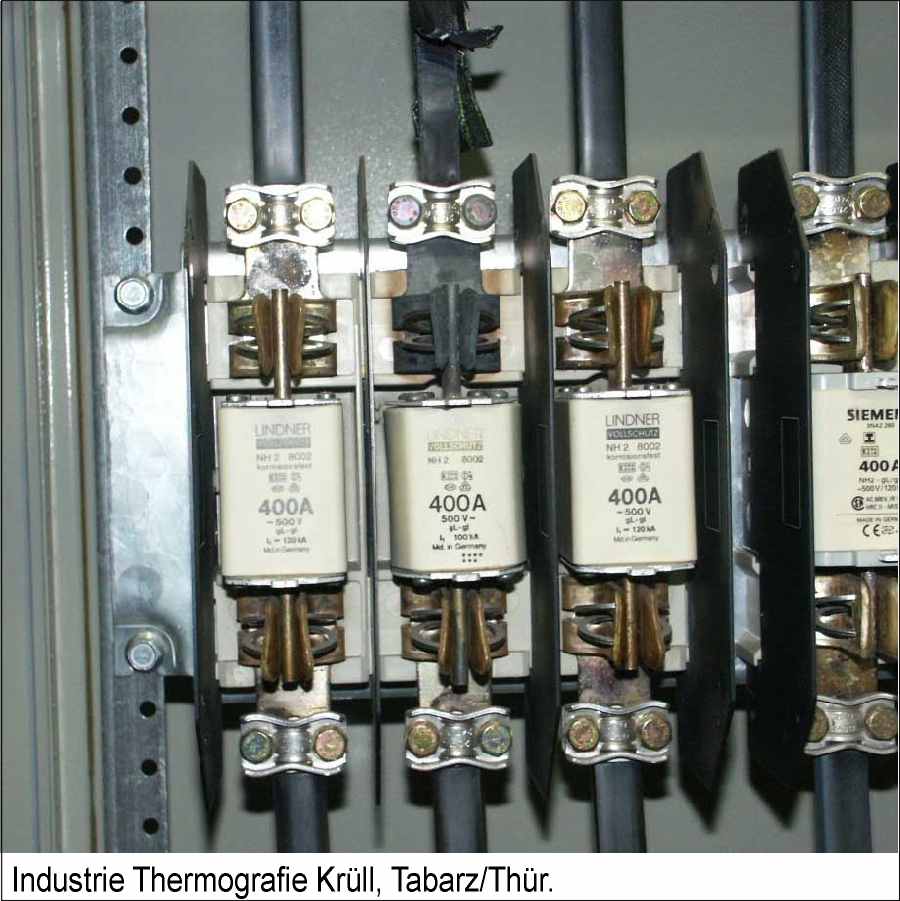
|
|
An diesem BD - System ist die Schienenverbindung
unter der Verkleidung nicht in Ordnung. 48,2°C ist
zwar noch nicht sehr warm, eine Schwachstelle liegt jedoch eindeutig vor.
Da eine Erwärmung mit Sicherheit auf die Dauer immer größer wird (siehe
die Erwärmung einer Fehlerstelle innerhalb eines Jahres um das Doppelte -
auf dieser Seite) besteht auch hier Handlungsbedarf.
|
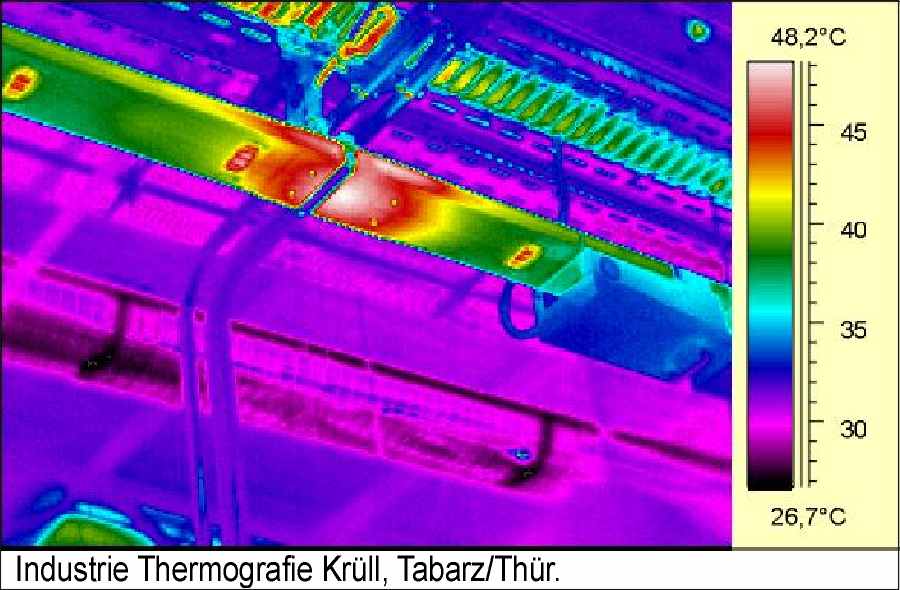
|
. . . . . . . .
|
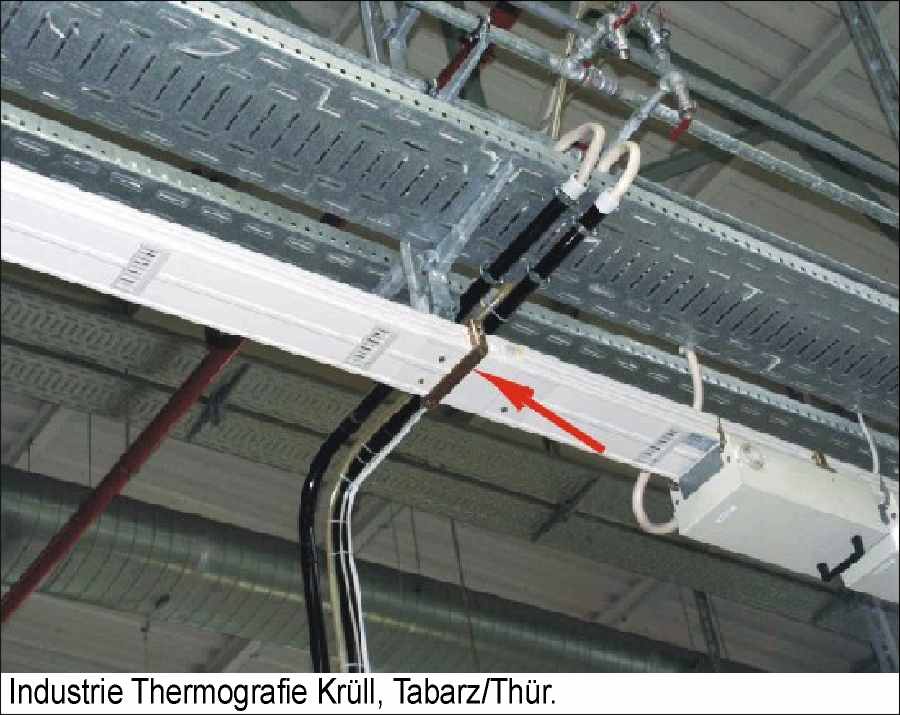
|
|
Die Zuleitung zu einem Kompressor ist am Abgang
dieses Leistungsschalters (Leiter L2) mit 423°C so heiß, dass ein Brand
nicht mehr lange zu vermeiden gewesen wäre. Der Abgang war erst vor einem
Jahr in Betrieb genommen worden. Ein entstandener Grat beim Aufbohren des
Kabelschuhes wurde bei diesem Beispiel nicht entfernt. Ein gleichmäßiges,
flächenhaftes Aufeinanderliegen der Kontaktflächen wurde somit
verhindert. Die so entstandene Querschnittsschwächung
hat die starke Erwärmung hervorgerufen. Eine fast 100 %ige Einschaltdauer bei einer gleichbleibenden
Belastung von ca. 210A hat die Schraube der eigentlichen Verbindung zum
Glühen gebracht. Dieser Schraubenkopf ist nicht direkt einsehbar, da er
an der abgewandten Seite des Kabelschuhes liegt. Der glühende
Schraubenkopf spiegelte sich allerdings schon, bereits mit dem bloßen
Auge sichtbar, im verzinkten Blech des Schaltschrankes wieder. Durch die
hohe Temperatur am Anschluss des Leistungsschalters ist hier anzuraten
den gesamten Leistungsschalter auszutauschen..
|
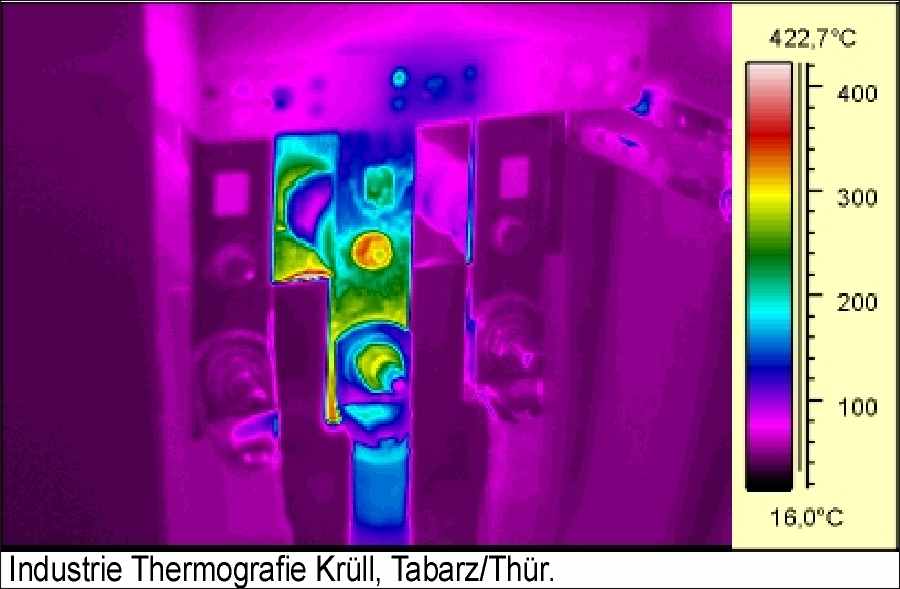
|
. . . . . . . .
|
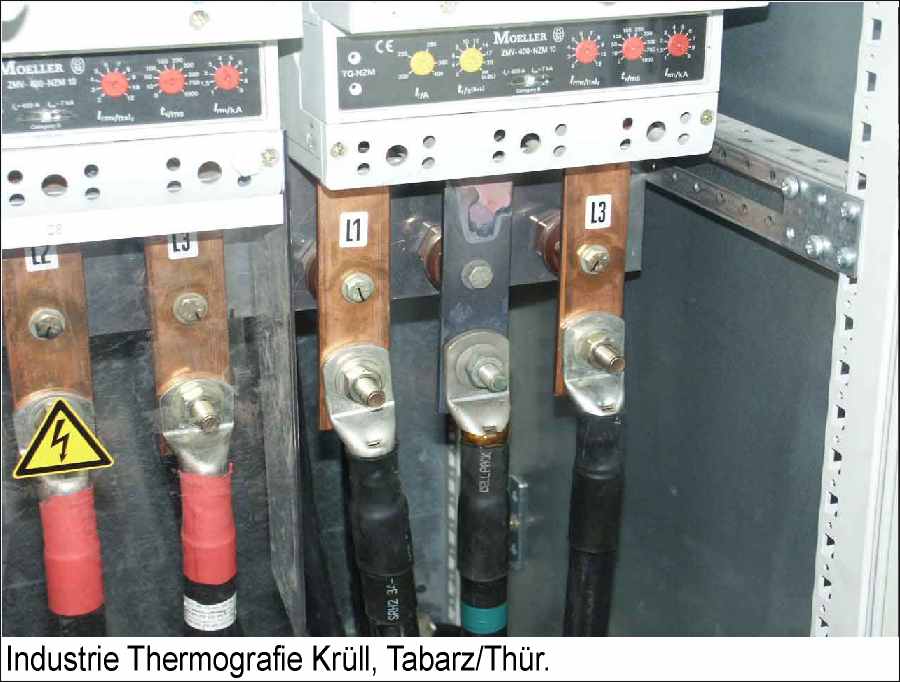
|
|
An diesem 110kV Leistungsschalter ist im Bereich
der oberen Löschkammer im Inneren ein fehlerhafter Bereich zu erkennen.
Bei der Graudarstellung könnte man meinen, dass es sich um ein Foto und
nicht um ein Infrarotbild handelt. Solche fotorealistische radiometrische
Infrarotbilder mit allen Temperaturinformationen sind nur mit
hochauflösenden Infrarotsystemen möglich und mit LowCoast-
Geräten undenkbar.
|
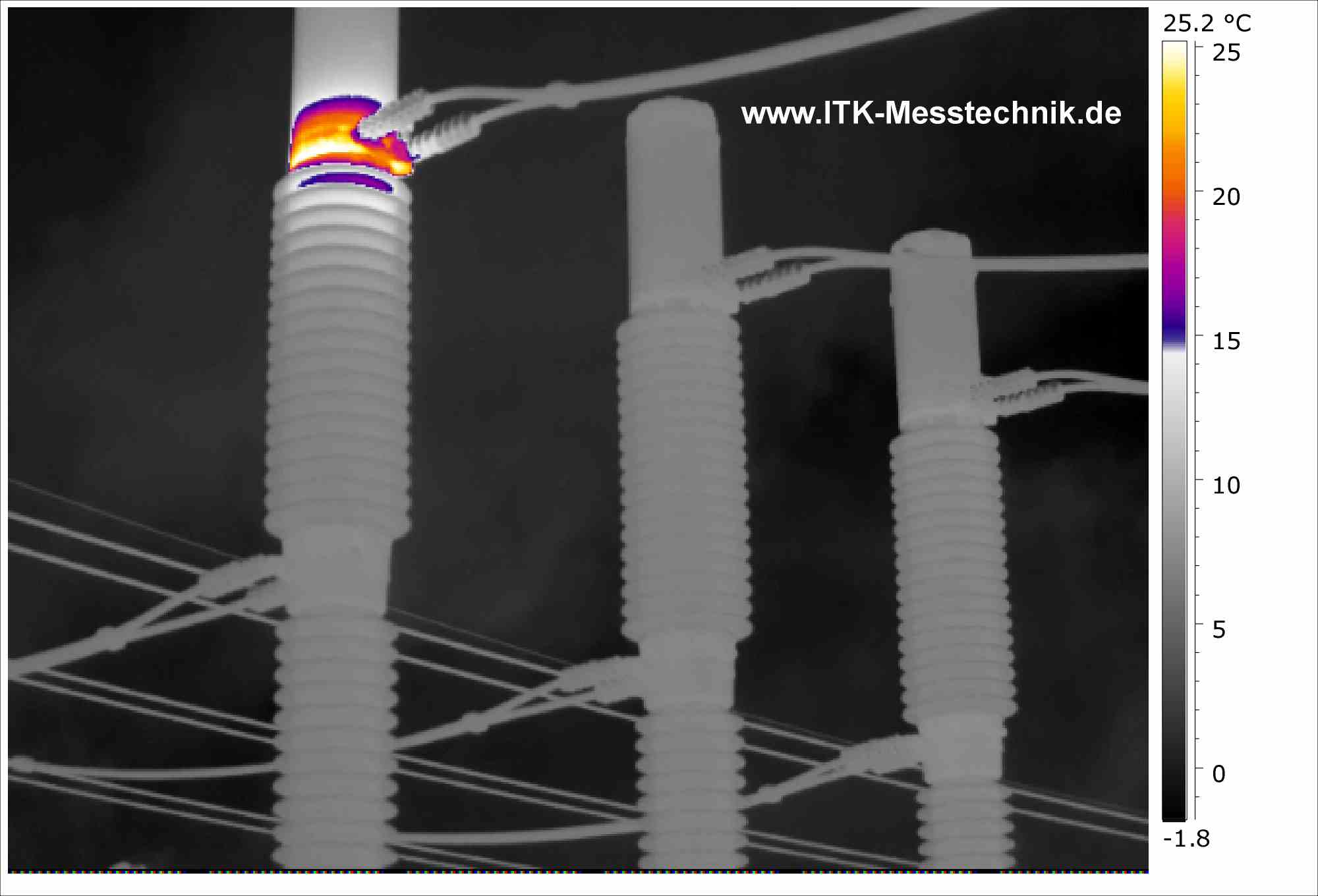
|
. . . . . . . .
|
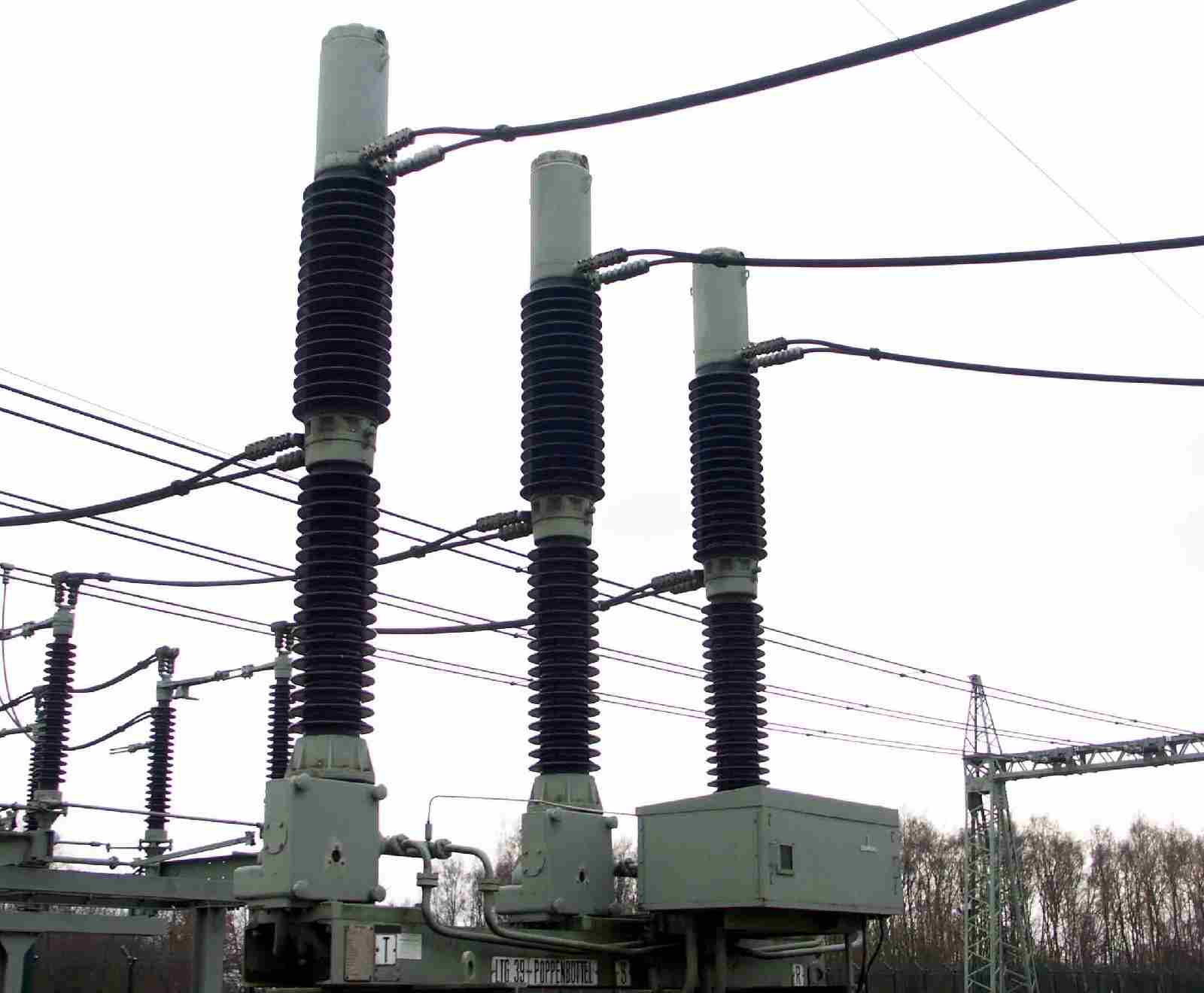
|
|
Die Feder für den Anpressdruck der Einfahrkontakte
dieses 110kV pantographen Sammelschienentrenners
ist gebrochen. An der Einschlagseite, direkt am Kontakt werden
Temperaturen von 235°C gemessen. Auf der Rückseite sind es sogar 336°C.
Hier ist schon die verbrannte Farbe zu erkennen. Bei einer Belastung von
67% der Nennlast ergibt sich bei Hochrechnung
eine Temperatur von ungefähr 700°C. Dieser Trenner
wurde sofort außer Betrieb genommen und Teile ausgetauscht...
|
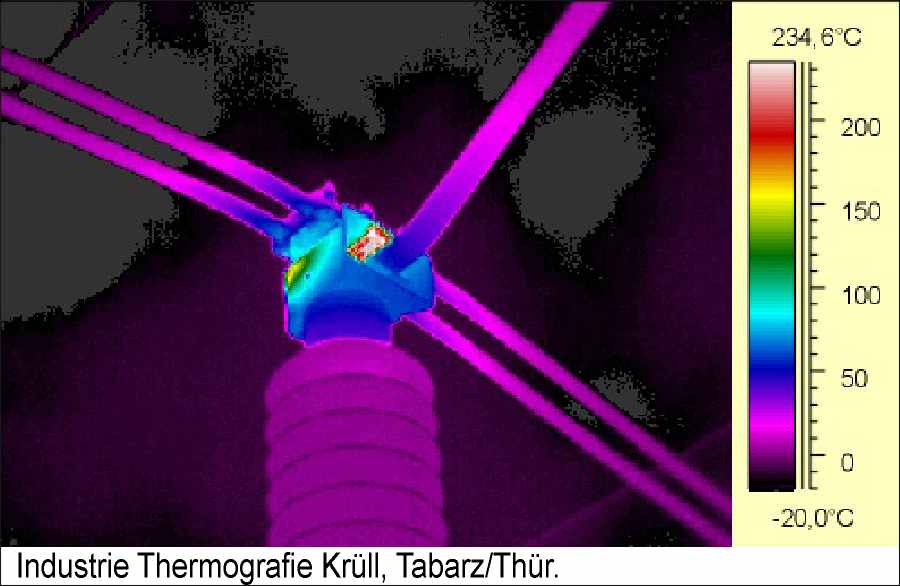
|
. . . . . . . .
|
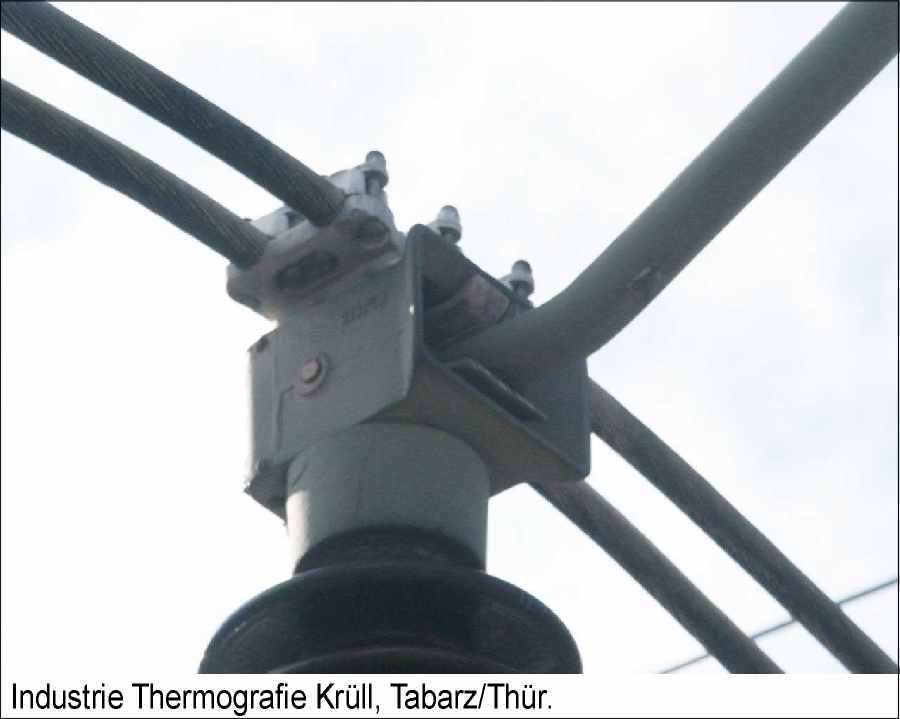
|
|
|
|
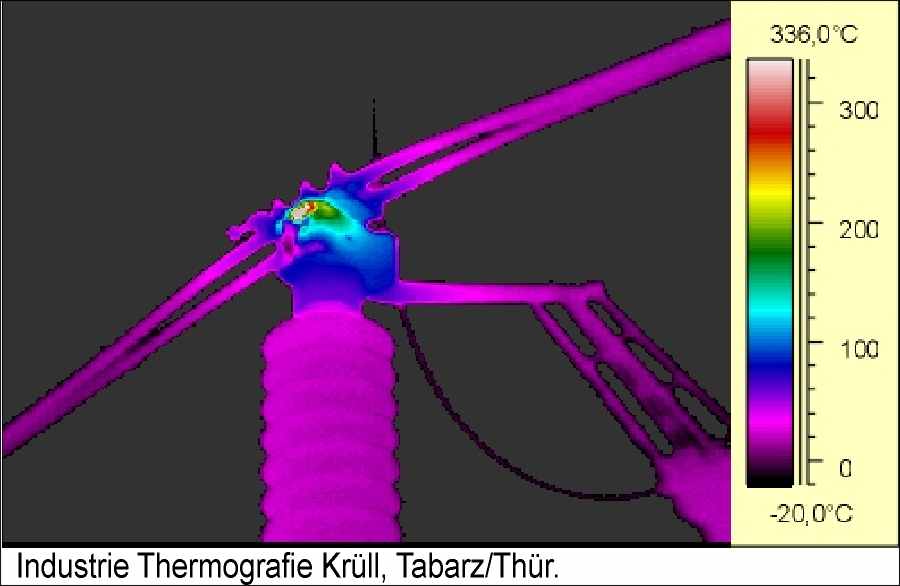
|
. . . . . . . .
|
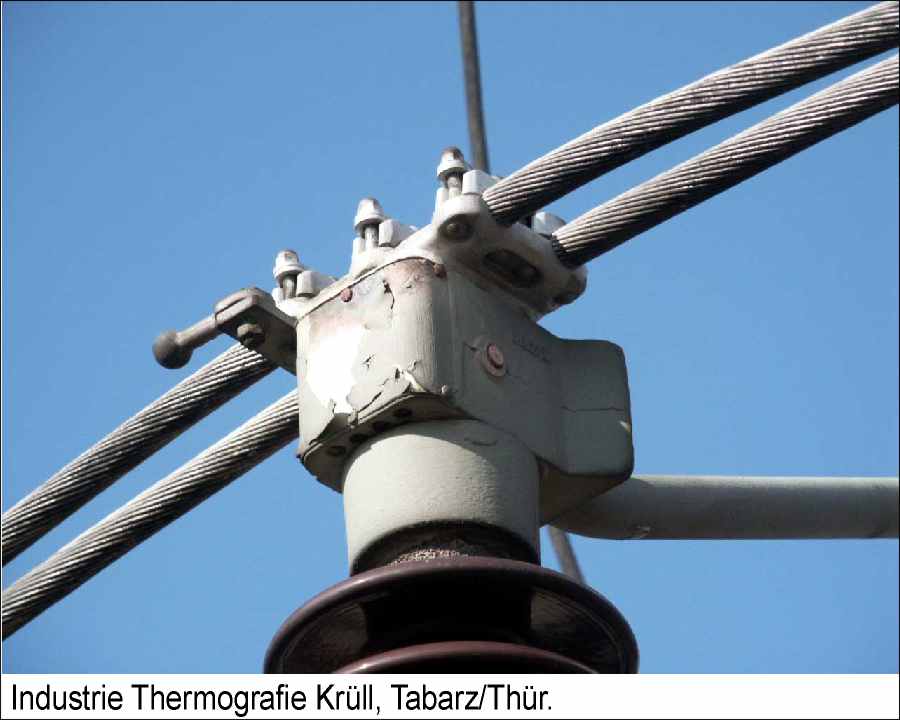
|
|
Bei diesem 380kV Überspannungsableiter
liegt nur die Spannung an. Einen Stromfluß gibt
es hier im Regelfall nicht. Trotzdem kommt es am Leiter L3 zu einer Erwärmung
des Kopfes. Die vergrößerte Darstellung mit dem 7° Infrarot- Teleobjektiv
bestätigt diese Erwärmung nochmals. Obwohl die Temperaturerhöhung nur 4°C
beträgt, wird diese mit geeigneter Infrarottechnik sicher lokalisiert. Mit
billigen Infrarotkameras sind derartige Fehlerstellen nicht zu finden.
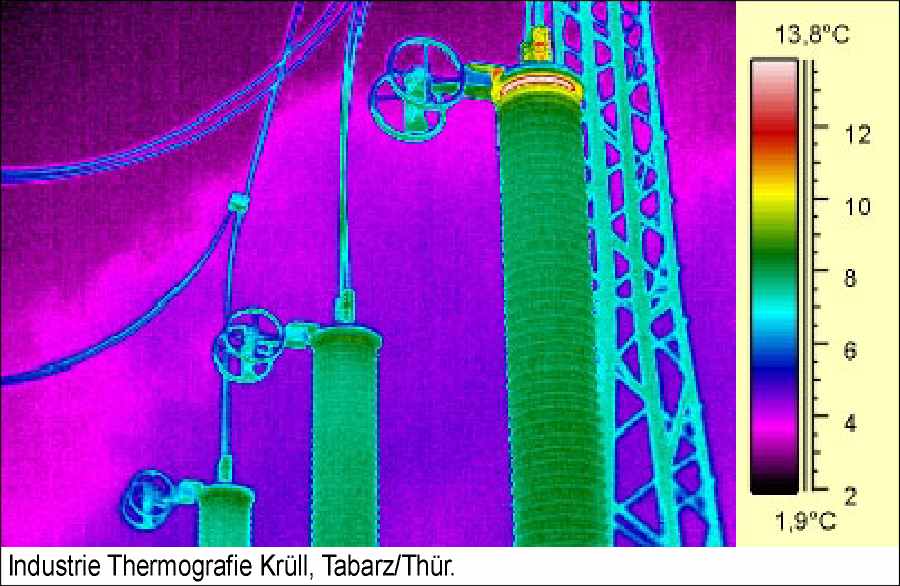
|
. . . . . . . .
|
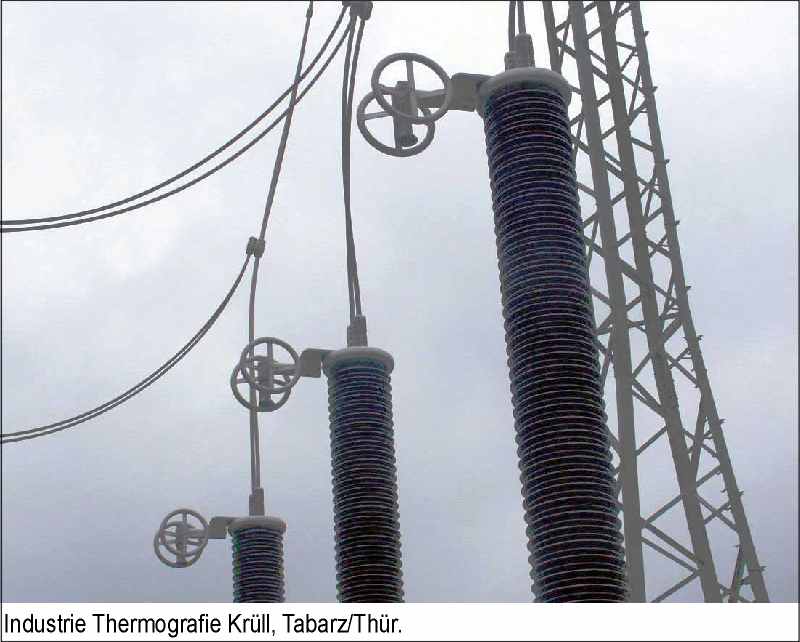
|
|
|
|
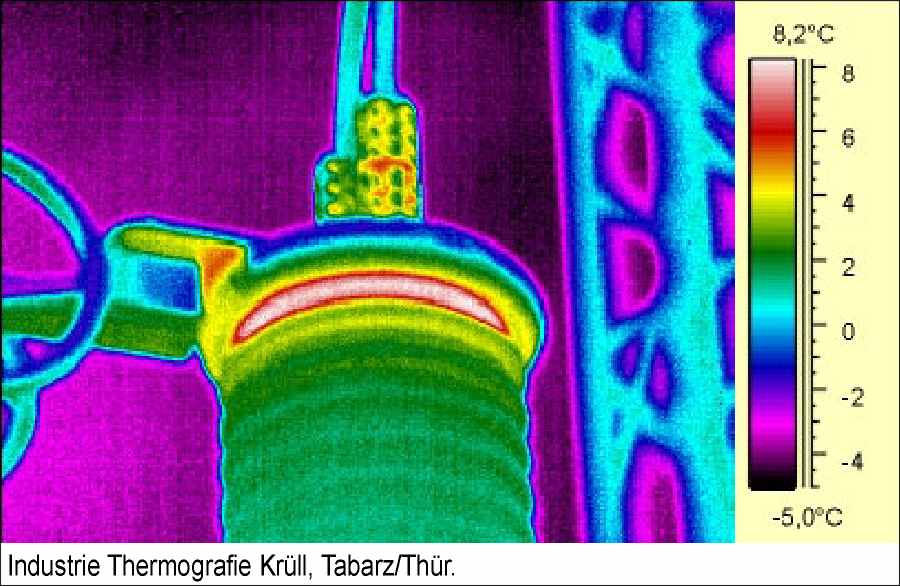
|
. . . . . . . .
|
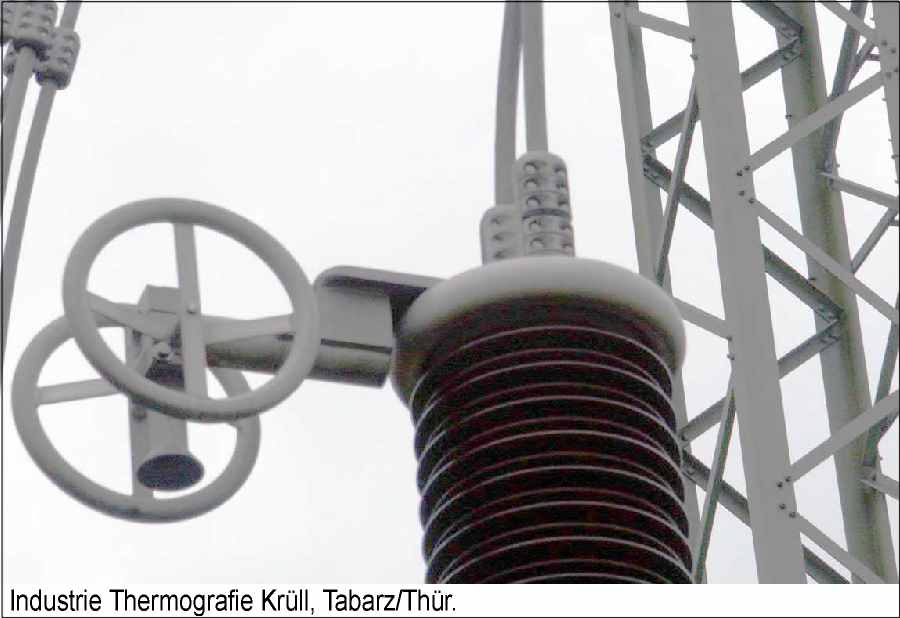
|
|
Im unteren Infrarotbild ist ein Flachanschluss an
einer 380kV Leistungsschalterverbindung dargestellt. Durch die große
Entfernung wäre diese detaillierte Aufnahme ohne Teleobjektiv nicht
möglich und eine genaue Zuordnung der Schwachstelle könnte nicht
erfolgen. Die thermische Schwachstelle besaß, zum Zeitpunkt der Messung,
eine Temperatur von 230°C bei nur 14% der Nennlast.
Rechnet man diese Temperatur auf den Grenzstrom hoch, so ergäbe sich eine
theoretische Temperatur von ungefähr 2.600°C. Diese hohe Temperatur würde
jedoch nie erreicht, da das Aluminium des Flachanschlusses bereits bei
ca. 600°C (Schmelzpunkt hängt von der Legierung ab) schmelzen würde. Auch
hier wäre es durch den Einsatz ungeeigneter Messtechnik zu Fehlmessungen
gekommen. Mit einer Kamera, welche keine hohen Temperaturen erfassen
kann, könnte die Temperatur gar nicht erst gemessen werden und ohne
geeignetes Teleobjektiv oder nur mit einem kleinen Bildschirm bei starker
Sonneneinstrahlung (wie bei den preisgünstig angebotenen Infrarotkameras)
hätte man den Fehler auch nicht erkannt. Das hätte in der Folge zu
schwerwiegenden Schäden und großflächigen Stromausfällen führen können.
Bei allen Messungen in den Umspannwerken, aber auch in
Industriebetrieben, lastet eine sehr hohe Verantwortung auf dem Messingenieur und das beauftragende
Energieversorgungsunternehmen oder die technischen Leiter in den
Industriebetrieben müssen sich stets voll auf die Messungen verlassen
können. Aus diesem Grund ist eine, dem Verwendungszweck angemessene
Kameratechnik genau so wichtig, wie eine
ausreichende Qualifizierung und Zertifizierung der mit den Messaufgaben beauftragten Messingenieure.
Der Prüfingenieur zur Überprüfung von Elektroanlagen sollte Berufserfahrungen
aufweisen und muss eine Elektrofachkraft nach DIN VDE 0105-100 sein. Er
sollte die Zertifizierung zur Untersuchung von Elektroanlagen Stufe 2
nach DIN EN 473 besitzen, da nur diese zum selbstständigen Arbeiten ohne
Anleitung berechtigt. Weiterhin ist ein Nachweis zum VdS
anerkannten Sachverständigen für Elektrothermografie zur Untersuchung
elektrischer Anlagen anzustreben und wird von Versicherungen gefordert.
Nur diese Voraussetzungen führen zu einer hohen Fachkompetenz bei der
Messung und Beurteilung thermischer Erwärmungen, welche oft auch
bauteilbedingt und normal sind.
Ein Öffnung der Kontaktstelle mit anschließendem
Säubern und Fetten der Kontaktflächen und einem erneute Verschrauben
mittels Drehmomentschlüssel beseitigt die Schwachstelle in der Regel. Ein
reines Nachziehen der Schrauben bringt, bei diesen Flachanschlüssen, in
den seltensten Fällen den Erfolg. Hier ist weiter zu untersuchen, ob die
hohen Temperaturen nicht schon Schäden an den Teilen hervorgerufen haben.
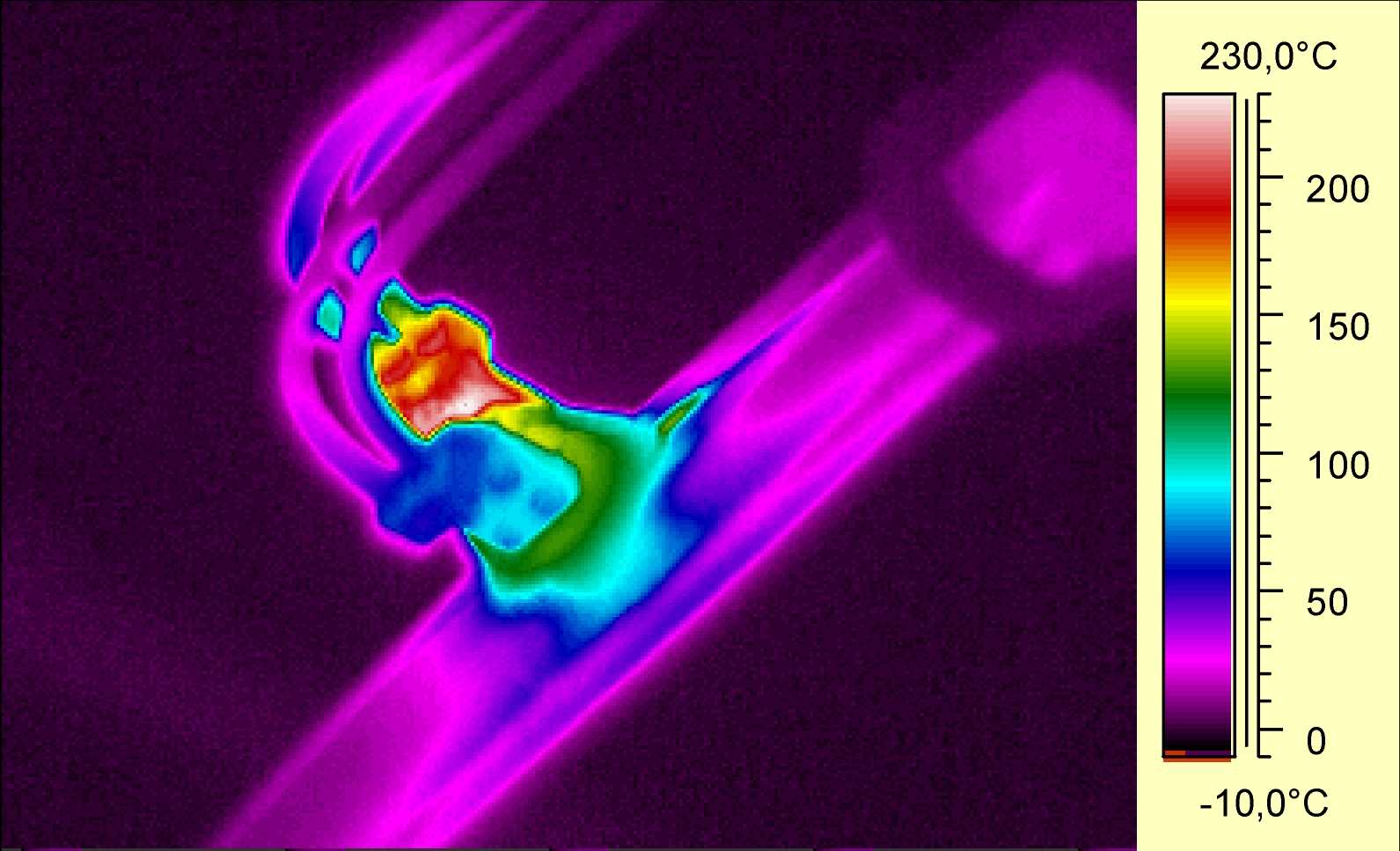
|
. . . . . . . .
|
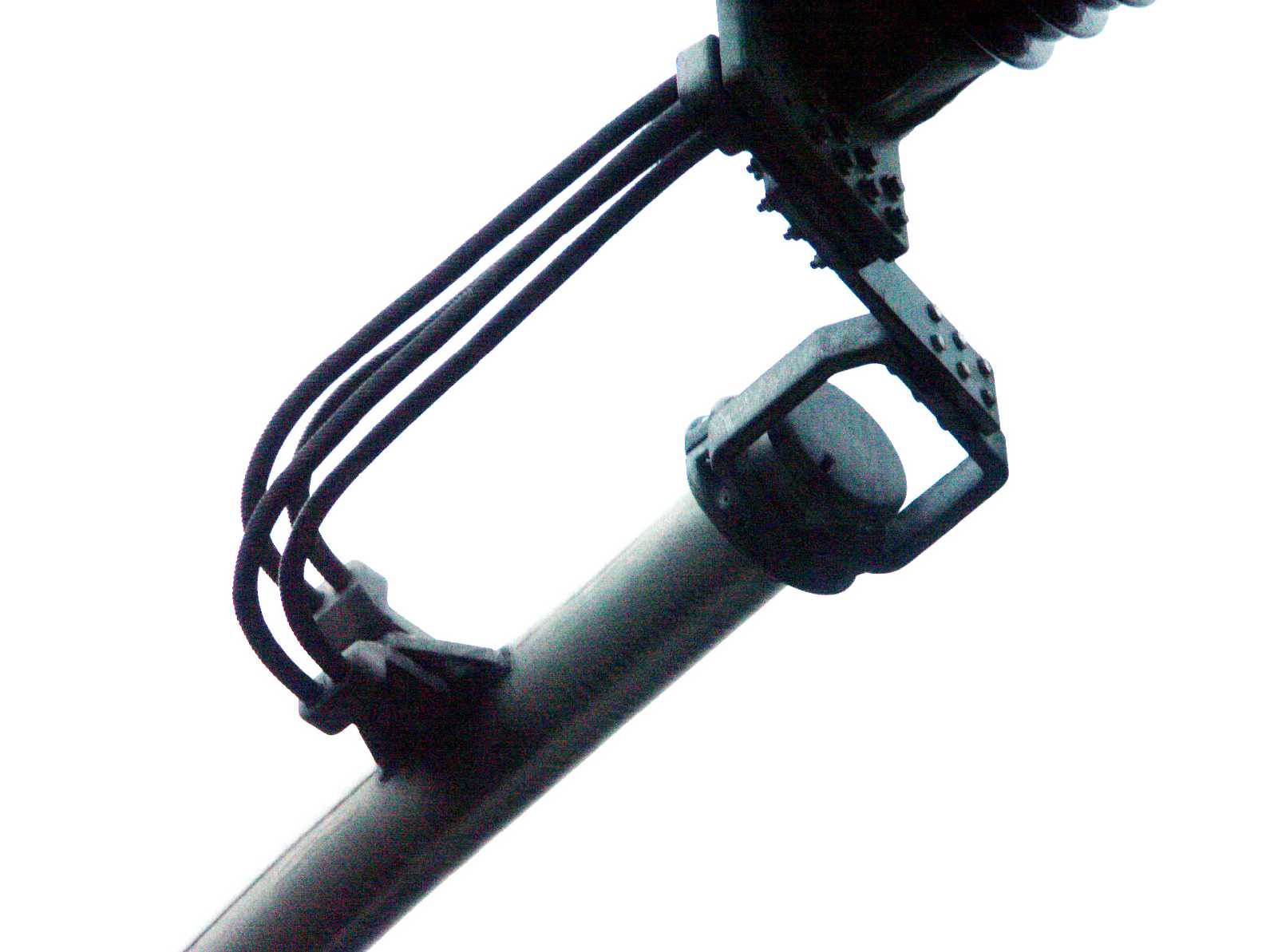
|
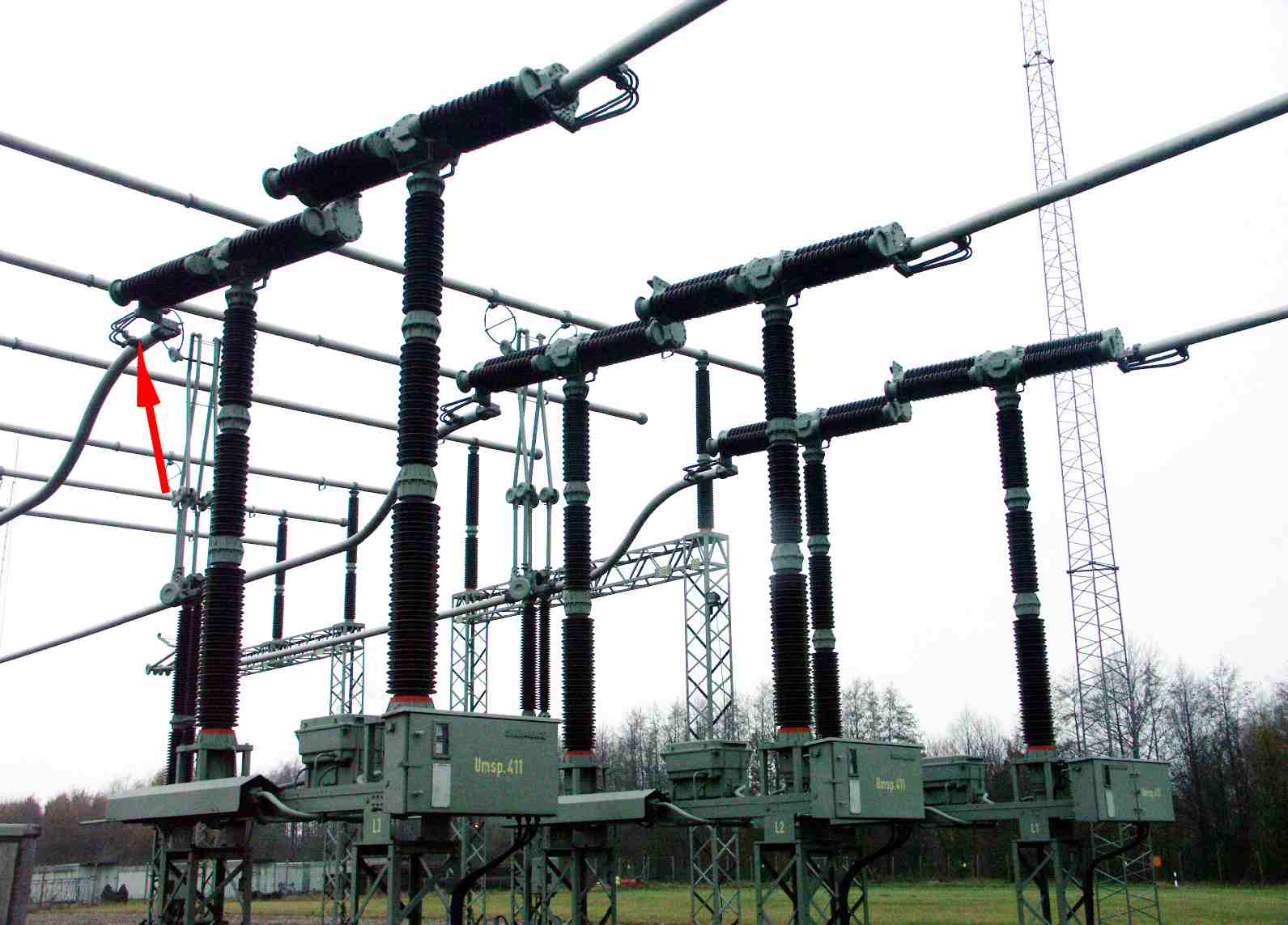
|
|
Durch einen ungenügenden Kontaktdruck an diesem
380kV Scherentrenner kam es bei dem unteren
Beispiel zu einer Erwärmung von über 104°C. Durch den großen Messabstand von 380kV Anlagen ist auch hier eine
detaillierte Aufnahmen nur mit einem 7° Infrarot- Teleobjektiv möglich.
Die Ursache für die Erwärmung kann neben dem ungenügenden Kontaktdruck
auch die Oberflächenbeschaffenheit der Kontaktstellen sein.
Einbrennstellen oder Oxidschichten können den Übergangswiderstand so
stark erhöhen, dass es zu einer solchen Erwärmung der Bauteile kommt.
Durch die Messung in die Atmosphäre kommt es in diesem Infrarotbild zu
der tiefen Temperatur von über -60°C (wolkenloser Himmel).
|
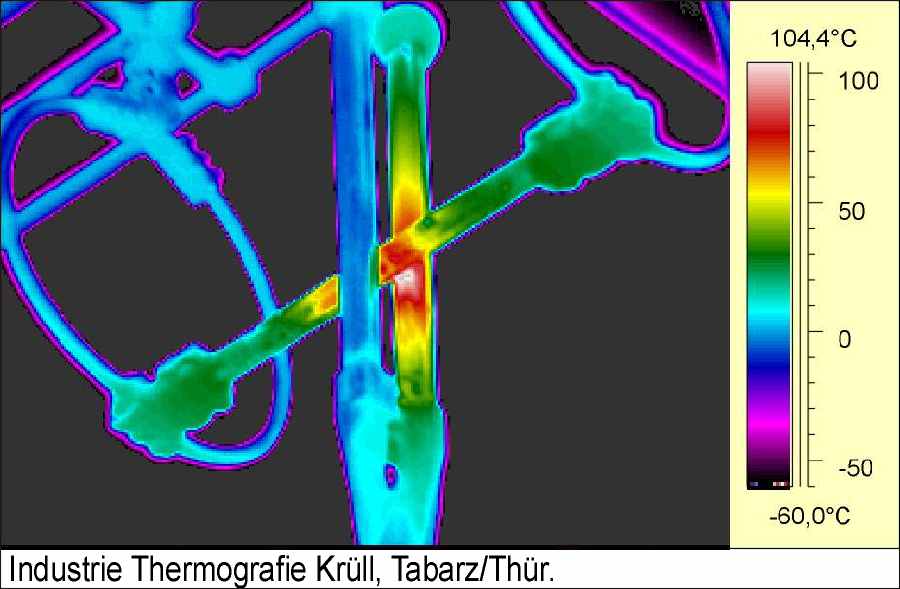
|
. . . . . . . .
|
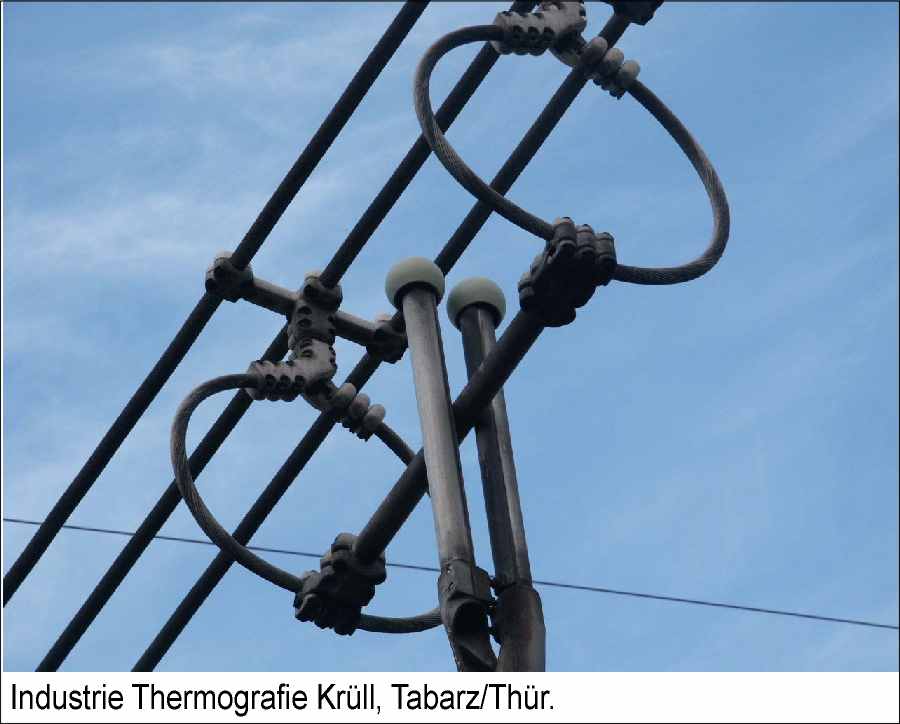
|
|
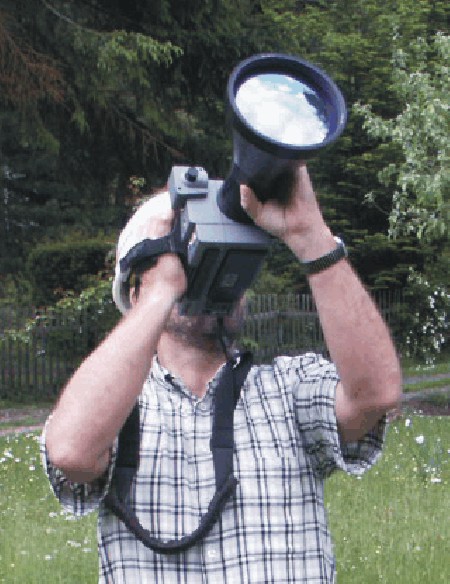
|
. . . . . . . .
|
Wie schon erwähnt, ist es zur Überprüfung von
Hochspannungsanlagen zwingend erforderlich, hochwertige Infrarottechnik
mit Teleobjektiven einzusetzen. Dies erklärt sich aus der geometrischen
Auflösung (IFOV - Instantaneous Field
Of View) einer jeden IR- Kamera.
Bei einer Messentfernung von 10 m beträgt diese
geometrische Auflösung, z.B. der ThermaCAM PM
695 mit einem 24° Objektiv 13 mm. Es ist also nur möglich einen Fehler in
10 m Entfernung exakt in seiner Temperatur zu messen, welcher eine
Ausdehnung von 13 mm nicht unterschreitet. Setzt man jetzt ein 7°
Teleobjektiv ein, so verbessert sich diese geometrische Auflösung auf 3,8
mm. Man kann mit einem Teleobjektiv also bedeutend kleinere Fehlerstellen
lokalisieren und in ihrer Temperatur exakt bestimmen. Die Unterschiede
der verschiedenen Objektive kann man an den beiden unteren älteren
Infrarotbildern 026 und 033 erkennen.
|
|
Auch die beiden unteren Infrarotbilder sollen
nochmals die Notwendigkeit eines Teleobjektives verdeutlichen. Hier
handelt es sich um eine 110kV T- Klemme in ca. 8m Höhe. Mit dem 7°
Teleobjektiv ist sehr genau erkennbar, welche Schraubverbindung, bzw.
Federblech an der Klemme fehlerhaft ist. Das weitere Infrarotbild wurde
mit einem 24° Normalobjektiv gespeichert. Hier ist nur zu sehen, dass die
T- Klemme fehlerbehaftet ist. Woran die Ursache für die Erwärmung liegt,
ist auf Grund der großen Messentfernung nicht
möglich.
Da Teleobjektive sehr preisintensiv sind, haben nur
wenige gleichgelagerte Büros diese Objektive zur Verfügung. Gerade bei
110kV, 220kV und 380kV Anlagen sind die Betrachtungsabstände sehr groß
und Teleobjektive sind nach unseren Erfahrungen
|
Die
linke untere Infrarotaufnahme einer 110kV T- Klemme wurde mit einem 24°
Normalobjektiv aufgenommen.
Hier werden 36°C gemessen.
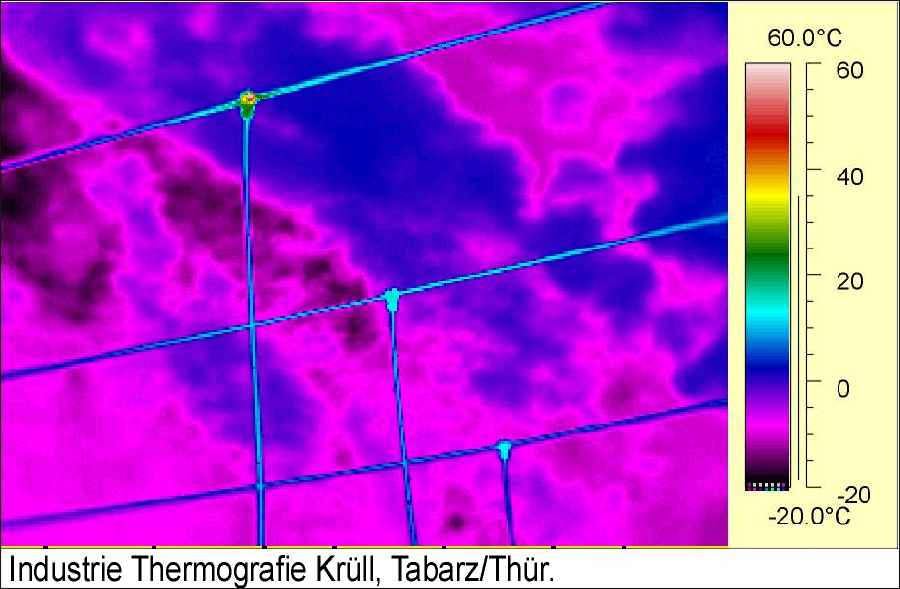
|
. . . . . . . .
|
Die
rechte Infrarotaufnahme der selben T-
Klemme wurde mit einem 7°
Teleobjektiv gespeichert. Das
IR- Bild zeigt eine Temperatur von 61,4°C.
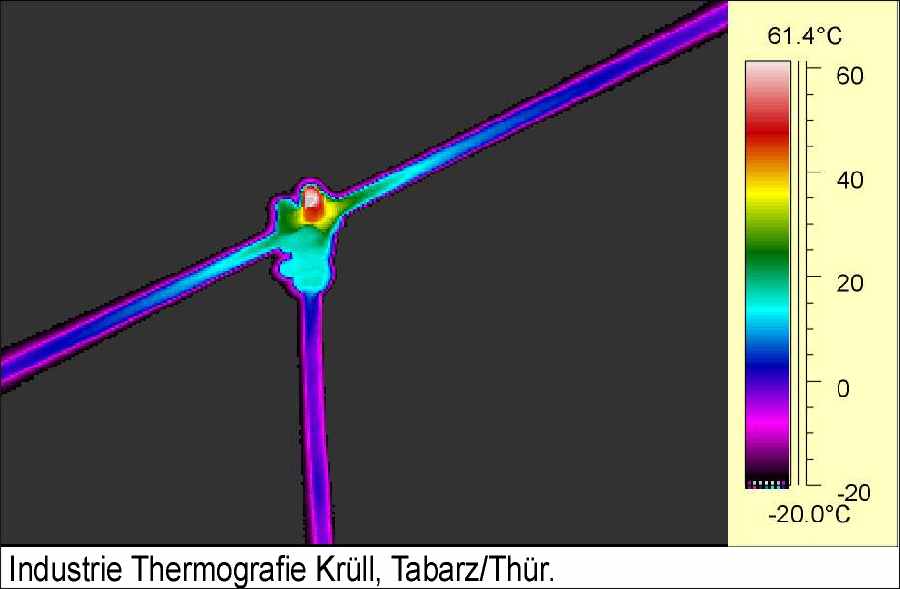
|
|
Werden ungeeignete Objektive verwendet, so kann es
zu gravierenden Fehlmessungen kommen, wie die beiden unteren
Infrarotbilder belegen. An dieser 110kV T- Klemme einer
Überspannungsverbindung ist mit einem Teleobjektiv eine von ihren Ausmaßen
sehr kleine aber prägnante Übertemperatur von 320°C zu messen. Mit einem
Normalobjektiv ist diese Fehlerstelle entsprechend des linken
Infrarotbildes auch zu erkennen. Die Temperatur wird durch die große Messentfernung und die geringen Ausmaße des
Übertemperaturbereiches um 124°C zu niedrig angezeigt. Der Grund dafür
ist in der eingangs erwähnten geometrischen Auflösung (IFOV) der
Infrarotkameras zu suchen. Man kann also nicht kleine Objekte in großen
Entfernungen mit ungeeigneten Objektiven messen wollen. Weitere solcher
Beispiele finden Sie in dem Zeitungsartikel "Hochspannungsanlagen
durch Infrarot- Thermografie optimal untersuchen" (430 KB).
|
|
|
|
Infrarotaufnahme
einer T- Klemme von einer Überspannungsverbindung mit einem
Normalobjektiv. Die größte gemessene Temperatur wir mit +196°C gemessen.
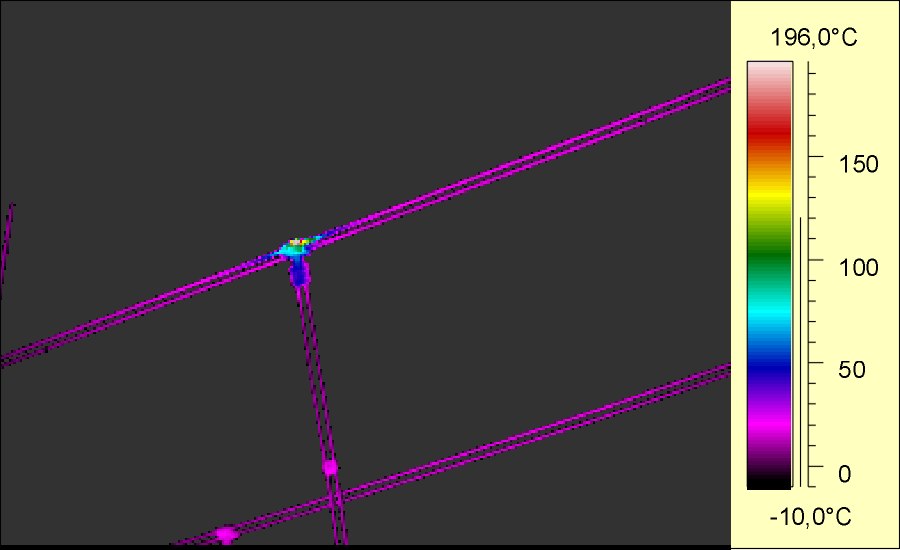
|
. . . . . . . .
|
Infrarotaufnahme
einer T- Klemme mit einem Teleobjektiv. Die größte gemessene Temperatur
wir mit +320°C gemessen,
obwohl die beiden dargestellten IR- Bilder die gleiche Klemme zeigen.
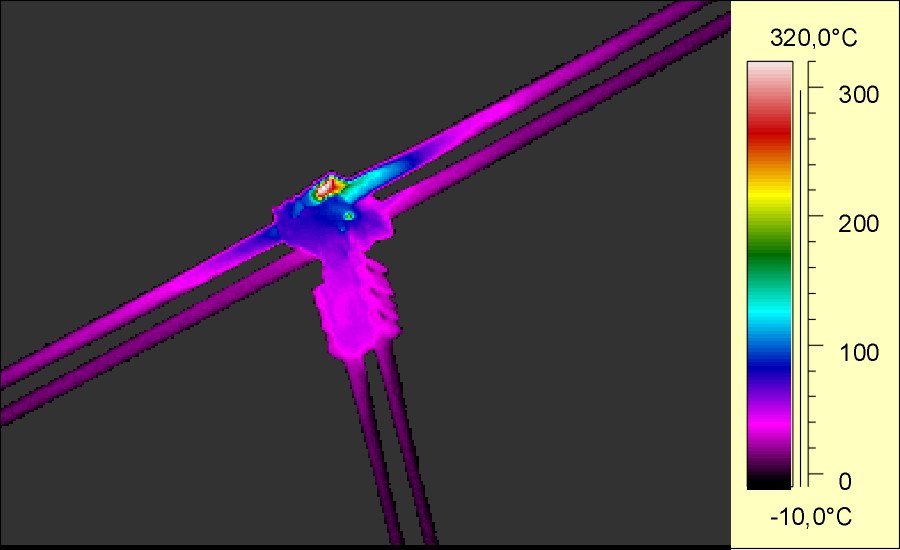
|
|
|
|
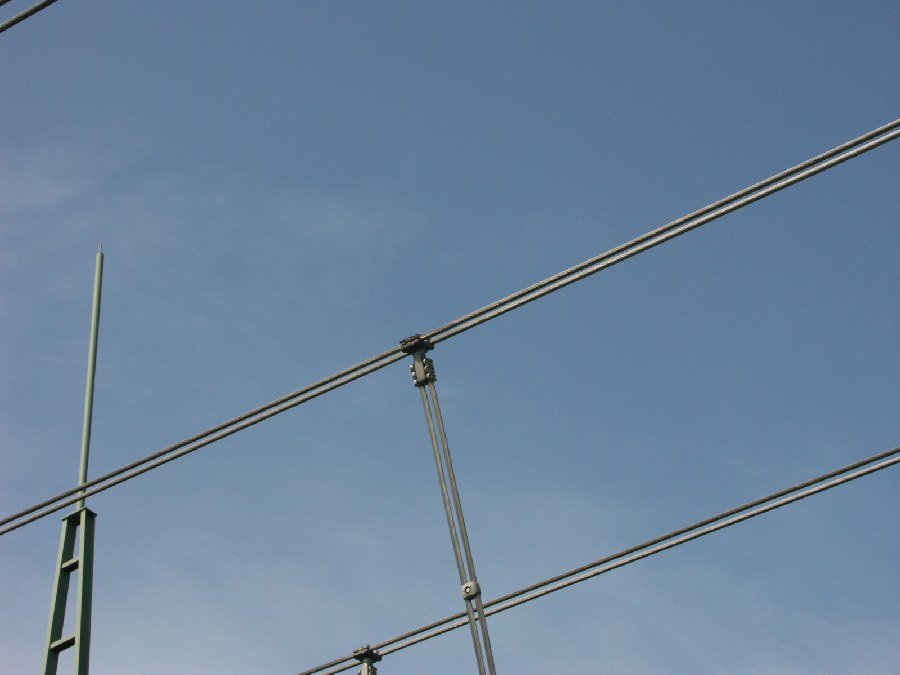
|
. . . . . . . .
|
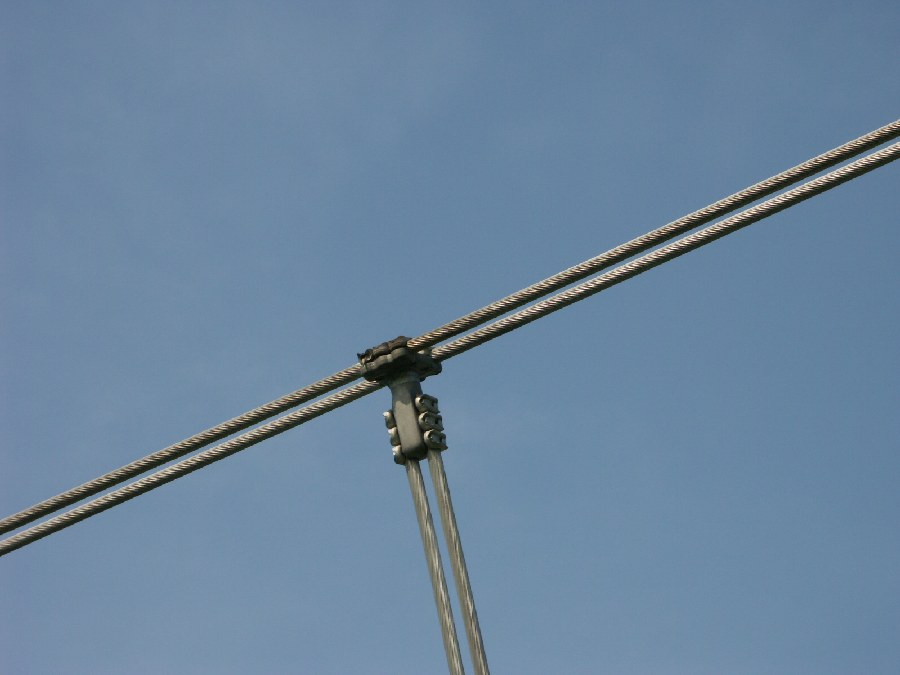
|
|
Um eine Einteilung der Fehlerstellen zu ermöglichen
wurde zur besseren Quantifizierung eine Fehlergruppeneinteilung entwickelt.
Die Übertemperaturen Delta (D) T werden somit in nachfolgende 4
Fehlergruppen unterteilt:
|
Fehlergruppeneinteilung
bei gemessener Übertemperatur DT in K
|
Temperatureinteilung
|
0 K < DT < 10 K
|
10 K < DT < 35 K
|
35 K < DT < 70 K
|
DT >
70 K
|
Fehlergruppe
|
Fehlergruppe 1
|
Fehlergruppe 2
|
Fehlergruppe 3
|
Fehlergruppe 4
|
Maßnahmen
|
keine
Maßnahmen, Nachbesserung innerhalb eines Jahres
|
Überprüfung der
Ursachen einschließlich Beseitigung bei der nächsten Wartung
|
Überprüfung der
Ursachen einschließlich Beseitigung bei einer Abschaltung, mindestens
< 1 Monat
|
kurzfristige Außerbetriebnahme,
Überprüfung der Ursache einschließlich Beseitigung, keine hohen
Belastungen
|
|
Unter dem Gesichtspunkt der notwendigen Inspektion
von Elektroenergieanlagen und des Brandschutzes sowie der Sicherheit und
der Versorgungszuverlässigkeit sind thermografische Messungen von
unbestreitbarem Nutzen. Es werden dadurch Zustände sichtbar gemacht, die
für das menschliche Auge unsichtbar bleiben würden. Durch die Lokalisierung
von Fehlerstellen können rechtzeitig punktgenaue Instandsetzungsmaßnahmen
eingeleitet und somit Folgeschäden vermieden werden und die Ausfallquote
sinkt erheblich. Darüber hinaus ergeben sich wirtschaftliche Nutzeffekte,
die von den Brandschutzversicherungen auch noch honoriert werden. Ob in der
Energieerzeugung, - weiterleitung oder - verteilung führen turnusmäßige IR- Messungen zu
nachweisbar höherer Sicherheit und nahezu uneingeschränkter Verfügbarkeit
beim Betreiben von elektrischen Anlagen.
Größtenteils treten die Erwärmungen durch eine
Erhöhung der Übergangswiderstände innerhalb der Verbindungen auf. Werden
beim Verbinden zweier Strombahnen die Leiter mit einer Kraft aufeinander
gedrückt, so ergeben sich aufgrund der Rauheiten
auf den Verbindungsflächen nur mikroskopisch kleine, die Kraft übertragende
Mikrokontakte, über die der Strom von einem Leiter zum anderen übertragen
werden kann. Dabei ergeben sich scheinbare (sichtbar), mechanisch tragende
und wahre Kontaktflächen (nicht sichtbar). Nur über die wahren/metallischen
und über die quasimetallischen Kontaktflächen, auf denen sich
Fremdschichten mit einer Dicke <2,5nm gebildet haben können, fließt der
Strom über die Kontaktflächen. Diese Fremdschichten müssen vor der
Verbindung der Kontakte aufgebrochen werden um den Gütefaktor zu erhöhen. Mittels
Drahtbürste und ca. 20-30 Bürstenstrichen sollten beide Kontaktflächen
bearbeitet werden. Ohne dann die Kontaktflächen mit den Fingern zu berühren
(evtl. Schweiß und somit wieder Oxidation), sollten sie zur Verhinderung
der Wassereindringung in die Kontaktfläche mit
einem säurefreien Fett bestrichen und zusammengefügt werden. Sind also
thermische Fehler an z.B. Fachanschlüssen vorhanden, so bingt
ein Nachziehen der Schraubverbindung in den überwiegenden Fällen keine
Verkleinerung des Übergangswiderstandes.
Der Gütefaktor ku gibt das Verhältnis
des Verbindungswiderstandes Rv zum
Widerstand RL des homogenen Leiters gleicher Länge lü (Überlappungslänge) an. Er ist ein Maß
dafür, wie viel mal mehr Verlustleistung in der
Verbindung gegenüber dem Leiter erzeugt wird. Bei neu montierten
Verbindungen sollte der Gütefaktor ungefähr 1 betragen. Für Verbindungen,
die eine Lebensdauer von mehr als 30 Jahren haben sollen, muss der
Gütefaktor ku < 1,5 sein.
Die pdf- Datei eines
Zeitungsartikels zum Einsatz der Infrarotmessungen in Nieder- und
Mittelspannungsanlagen, wie er in einigen Fachzeitungen wie "building & automation"
Heft 5/2003 - VDE Verlag, "Krankenhaus Technik + Management" Heft
10/2003 - pn verlag,
"Elektropraktiker" Heft 11/2003 - Verlag Technik Berlin, "eb Elektrische Bahnen" Heft 1-2/2004 - Oldenbourg Industrieverlag, "de - Der Elektro- und
Gebäudetechniker" Heft 6+7/2007 - Hüthig
& Pflaum Verlag oder "instandhaltung"
Heft 2+3/2007 - verlag moderne
industrie GmbH erschienen sind, können Sie sich
hier als pdf- Datei herunterladen: "Nieder- und
Mittelspannungsanlagen durch Infrarot- Thermografie richtig untersuchen"
(481 KB).
Eine weitere pdf- Datei
eines Artikels für die Zeitschrift "netzpraxis"
Heft 12/2006 und Heft 1/2007 - VWEW Energieverlag zum Thema "Hochspannungsanlagen
durch Infrarot- Thermografie optimal untersuchen" (430 KB) können
Sie sich ebenfalls herunterladen.
Die Zeitschrift "Elektropraktiker
veröffentlichte im März 2010 einen weiteren Artikel zu Thema Thermografie.
Hier geht es in erster Linie um Normen, Fehlergruppeneinteilungen und
notwendige Qualifikationen "ep
Thermografie 03 2010.pdf" (930 KB) oder direkt zur Seite der
Zeitschrift www.e-pages.dk\dms\152\56.
Durch die z.T. billig gewordene Kameratechniken und massiver
Werbekampagnen der Herstellerfirmen wird seitens der Betriebe oder
Energieversorgungsunternehmen immer öfters überlegt, ob eine eigene
Kameratechnik nicht eine wirtschaftlichere Lösung darstellt, als externe
Dienstleister heranzuziehen. Bei diesen Überlegungen geht man jedoch meist
nur von der billigen Kameratechnik aus, von der man aus Unwissenheit
glaubt, damit selbst Untersuchungen durchführen zu können. Was nicht
bedacht wird ist, dass eine Kameratechnik für komplexe Untersuchungen nicht
mit billigen Geräten vorgenommen werden kann. Hochspannungsanlagen mit
diesen Geräten untersuchen zu wollen ist unmöglich. Will man z.B.
Elektroanlagen fachgerecht, entsprechend den Forderungen der
Versicherungswirtschaft untersuchen, so finden Sie im Nachfolgenden eine
Kostenaufstellung: Messungen
mit eigener Kameratechnik.pdf (511 KB).
|
Freileitungsbefliegung:
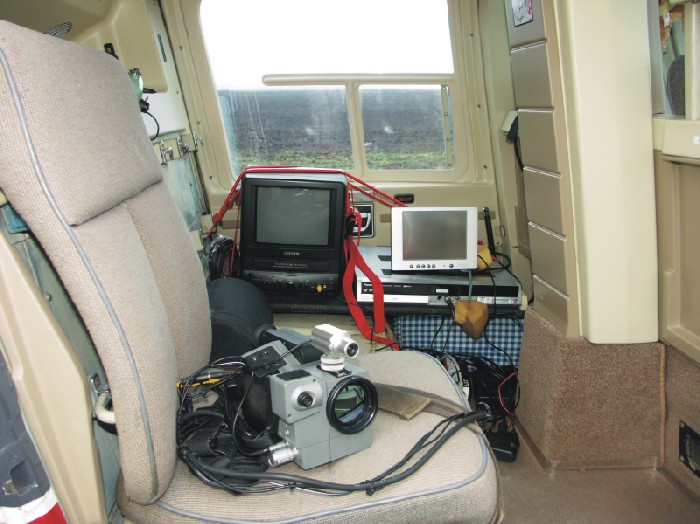
|
. . . . . . . .
|
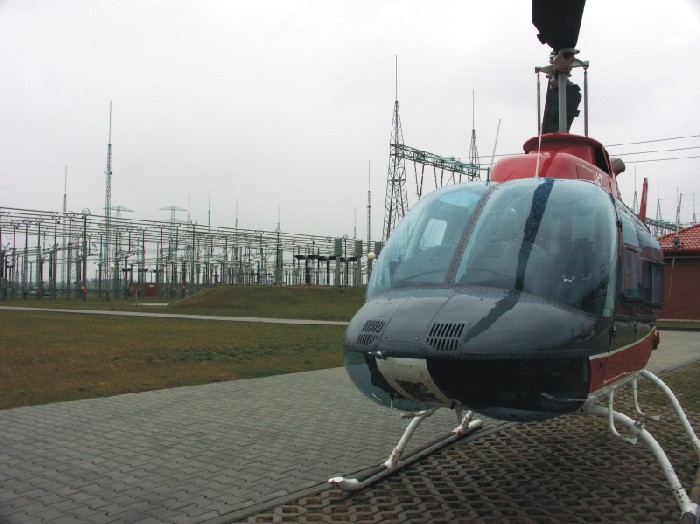
|
Freileitungen
im 110, 220 oder 380kV Bereich werden turnusmäßig einer Sichtkontrolle unterzogen.
Wegen der großen Leitungslängen von oft mehreren hundert Kilometern
werden diese von den Energieversorgungsunternehmen meist abgeflogen.
Neben der Sichtkontrolle werden ebenfalls Infrarotmessungen durchgeführt.
Lose und defekte Verbindungen an den Seilen können somit rechtzeitig
lokalisiert werden.
Im oberen Bild ist die Infrarotkamera mit Sichtbildkamera zu sehen.
Infrarot- und Sichtbild werden über je einen DVD Recorder kontinuierlich
gespeichert. 2 Monitore dienen zur Kontrolle der Bilder.
|
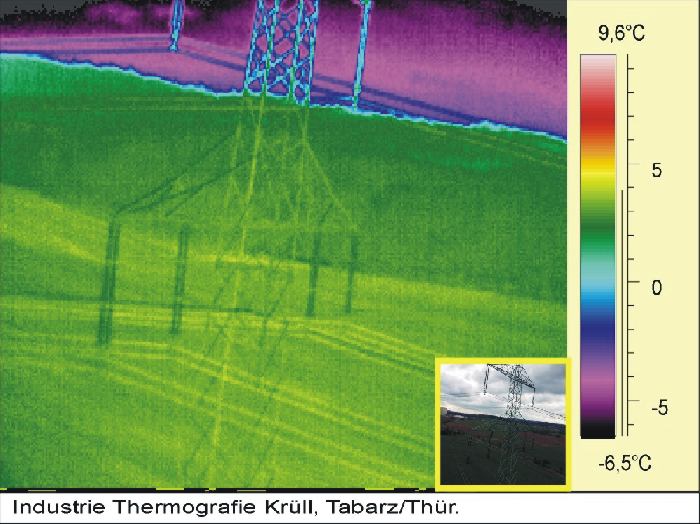
|
|
Mit einem neuen 4- Achsen
stabilisierten Kreiselsystem wird die Inspektion der Freileitungen noch
effektiver. Eine hochauflösende Infrarotkamera (640x480 Pixel) und eine
hochauflösende Kamera im sichtbaren Bereich speichern kontinuierlich
die Infrarot- und die Sichtbilder auf Festplatte. Die GPS- Daten werden
ebenfalls mit aufgezeichnet, wodurch die später einlesbaren
Daten in ein Kartensystem ein genaues Bild
der geflogenen Strecke wiedergeben. Die Bedienung erfolgt mittels
Tastatur und Joystick aus dem Helikopter. Sichtbild mit Uhrzeit und
GPS- Koordinaten und das Infrarotbild werden bei den Befliegungen der Freileitungen kontinuierlich auf
Festplatte gespeichert. Die spätere Auswertung erlaubt dann eine
parallele Abspielung beider Bilder im Rechner mit spezieller Software.
Die unteren beiden Bilder zeigen ein Sichtbild mit dem Infrarotbild von
einer 220kV Freileitung..
|
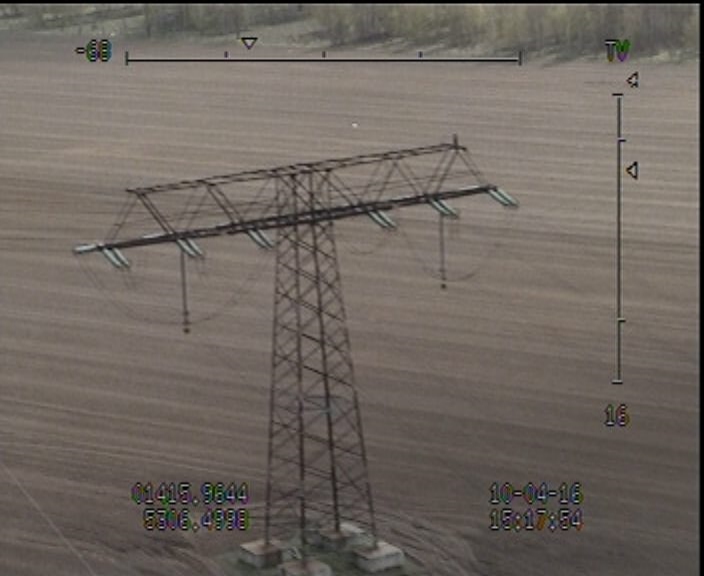
|
. . . . . . . .
|
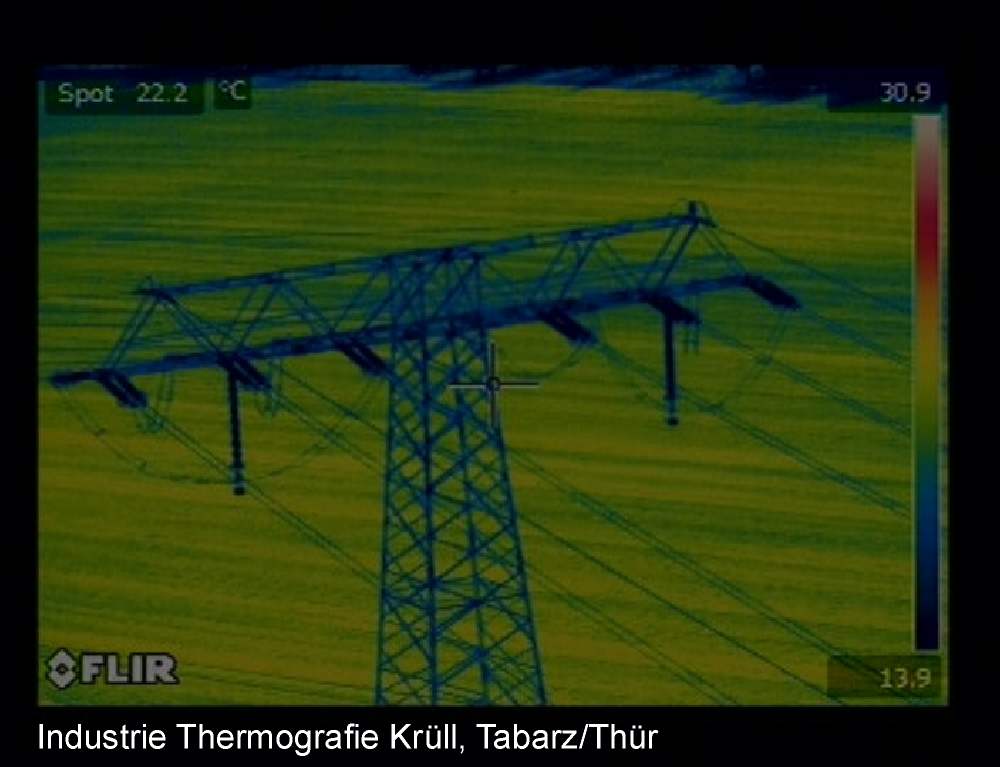
|
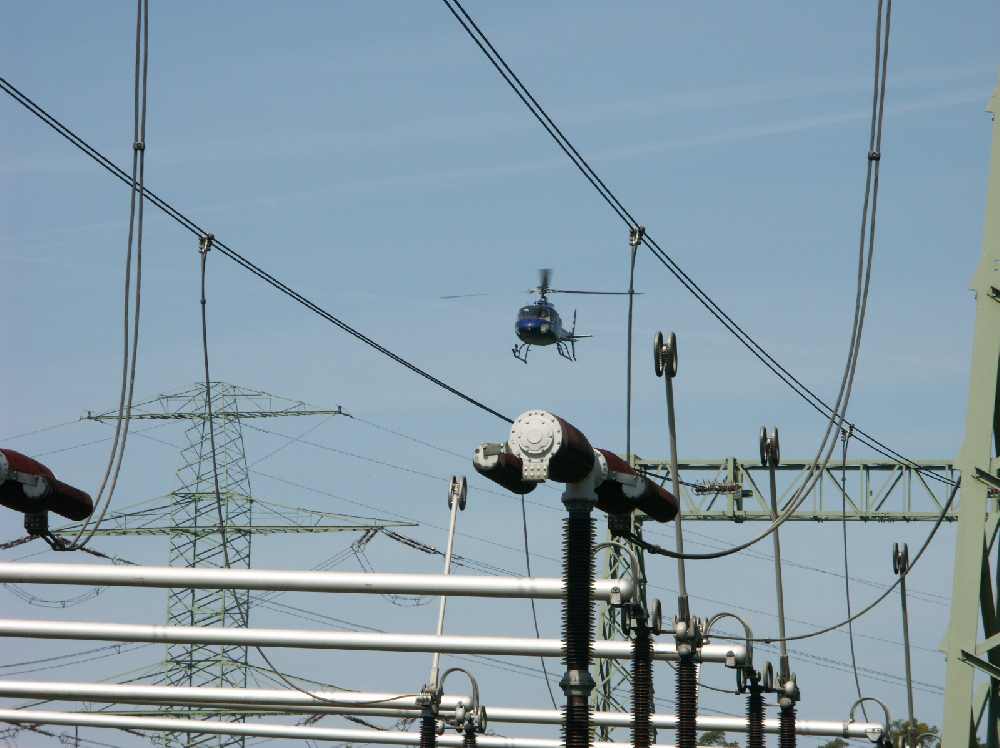
|
|
|
Über eine Korona- Kamera lassen sich Teilentladungen an
elektrischen Schaltanlagen detektieren .
|
|
|
|
|
|
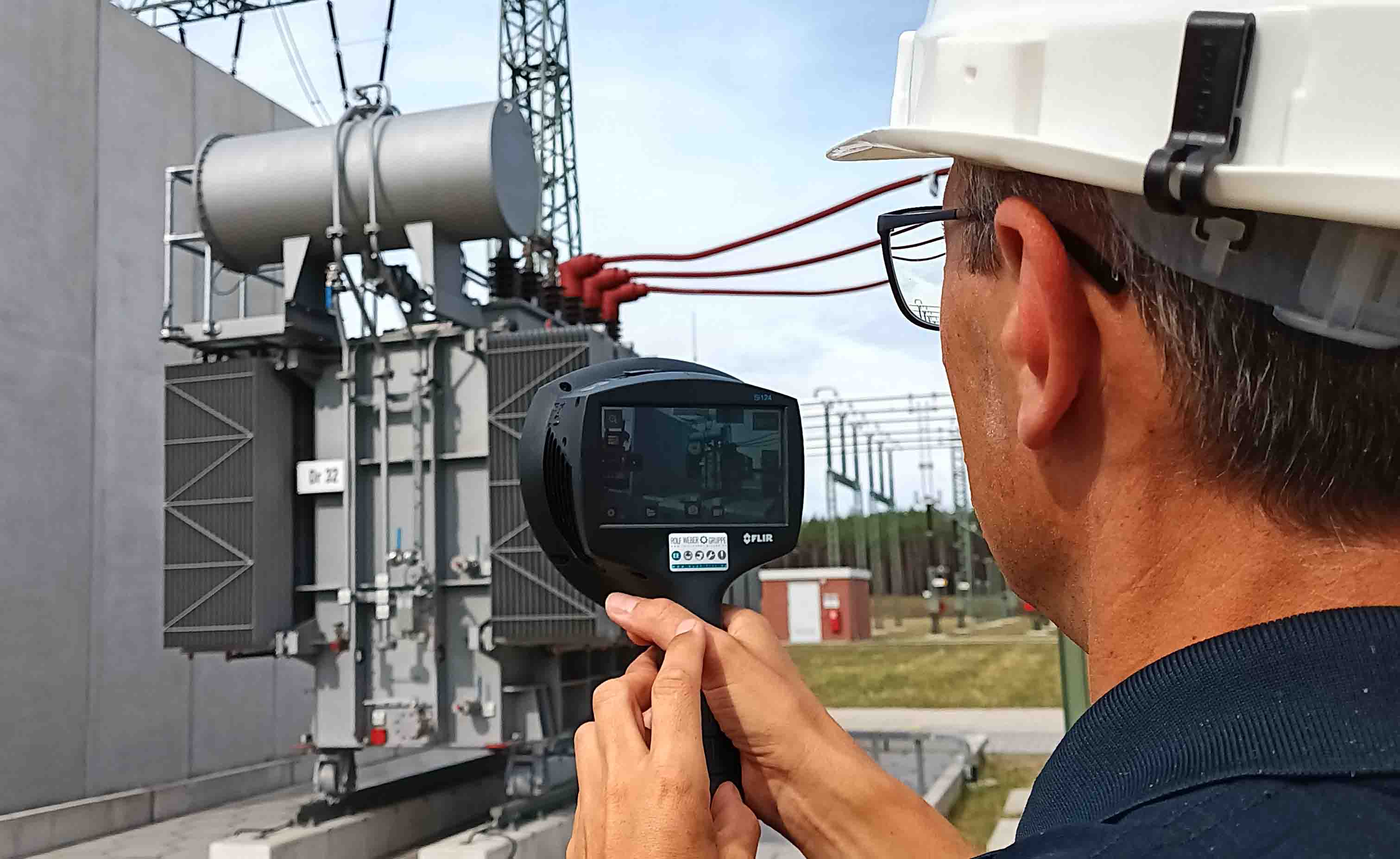
|
|
|
Wie z.B. Korona- Messungen an einem
380kV/110kV Transformator. Hier an der 380kV Trafodurchführung vom Leiter L2. .
|
|
|
|
|
|
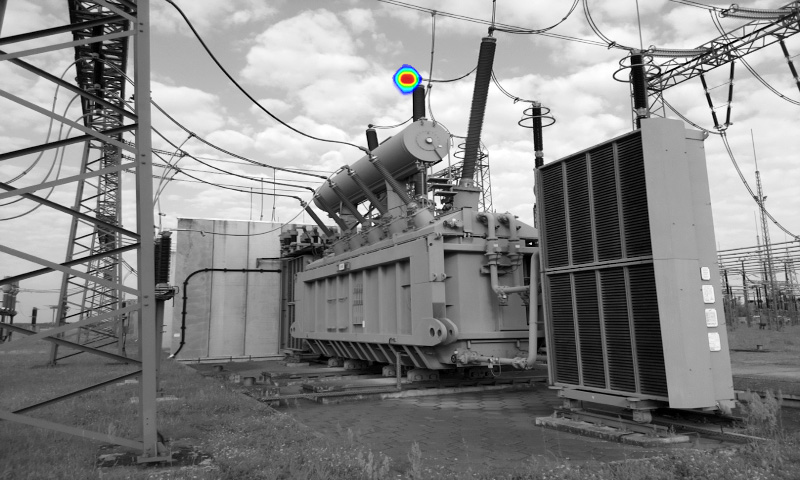
|
|
|
Oder an dem 220kV Überspannungsableiter vom Leiter L2. .
|
|
|
|
|
|
|
|
|